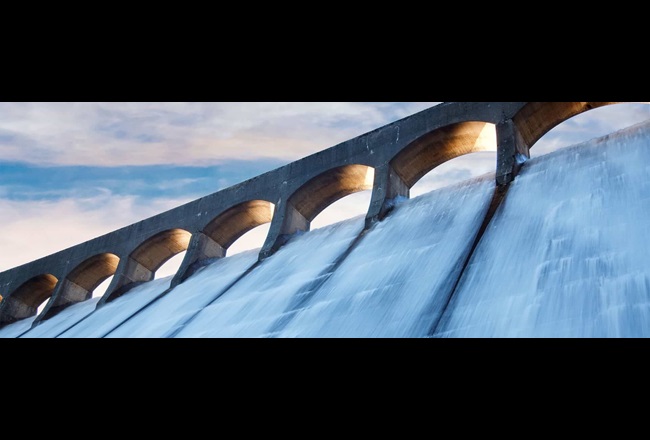
Umwelt im Fokus
Wir wollen auch bei der Reduzierung von Umweltbelastungen mit gutem Beispiel vorangehen. Das zeigt sich unter anderem in unserem verantwortungsvollen Umgang mit Wasser, Energie und Emissionen oder in der Nutzung alternativer Ressourcen.
Unsere Maßnahmen für eine nachhaltigere Produktion
Energie und Emissionen
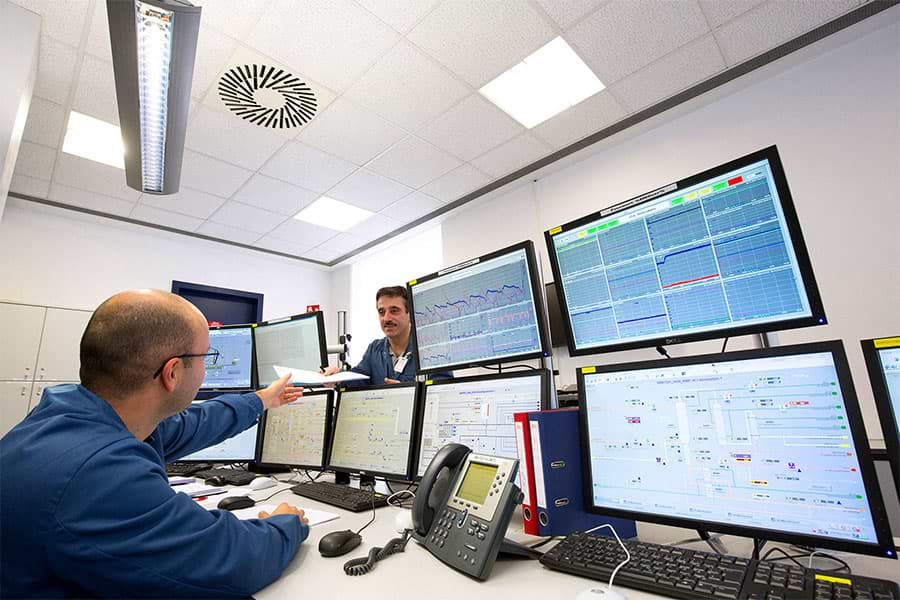
Unsere Prozesse verbrauchen große Mengen an Energie. Die chemische Industrie unternimmt deshalb alles, um ihre Effizienz zu optimieren und die Umweltbelastung der eigenen Produktion zu minimieren. Covestro übernimmt dabei eine Vorreiterrolle und hat ein System entwickelt, mit dem der Energieverbrauch von Anlagen individuell gemessen und gemanagt werden kann. So können wir sicherstellen, dass so wenig Energie wie möglich verbraucht wird. Dank des Systems „STRUCTese™“ konnten wir seit seiner Einführung im Jahr 2008 den Energieverbrauch unserer Werke um durchschnittlich zehn Prozent senken.
Eine der Besonderheiten dieses Systems besteht darin, dass der Energieverbrauch jeder einzelnen Anlage durchgehend online aufgezeichnet und mit einem errechneten Optimalwert verglichen wird. Expertenteams ermitteln zudem die Energieeffizienz der Anlage, legen einen Status und Verbesserungspotentiale fest und erstellen Aktionspläne.
Heute verwenden wir STRUCTese™ in 58 Werken in Europa, Asien und Amerika. Insgesamt hat der Einsatz dieses Systems dazu geführt, dass Covestro mittlerweile jährlich rund 600.000 Tonnen Treibhausgasemissionen weniger verursacht und rund 1,83 Terrawattstunden Primärenergie pro Jahr weniger verbraucht. Das ist in etwa so viel Strom, wie ca. 400.000 Windkrafträder in einem Jahr produzieren. Für die erfolgreiche Entwicklung und Umsetzung von STRUCTese™ wurde Covestro als Finalist in der Kategorie „Industrie“ der Handelsblatt Energy Awards 2016 nominiert. Darüber hinaus wollen wir bis 2030 den spezifischen Energieverbrauch unserer Produktionswerke im Vergleich zu 2005 ebenfalls halbieren. Diese Verdopplung unserer Energieeffizienz wird erheblich zur Reduktion spezifischer Treibhausgasemissionen beitragen.
Im Jahr 2017 konnten wir unseren spezifischen Energieverbrauch weiter reduzieren, und zwar um 2,9 Prozent im Vergleich zum Vorjahr. Im Vergleich zu 2005 stellt dies eine Verbesserung um 36,4 Prozent dar. Auch in diesem Fall verdanken wir unseren Erfolg dem Energieeffizienzsystem STRUCTese™. Im selben Zeitraum konnten wir unsere Treibhausgasemissionen (CO2-Äquivalente) um 43,8 Prozent senken. Im Jahr 2017 haben wir 4,9 Prozent weniger Treibhausgasemissionen verzeichnet als im Vorjahr.
Dazu tragen auch Prozessinnovationen bei: So haben wir einen Prozess zur Herstellung von Chlor entwickelt, bei dem die so genannte Sauerstoffverzehrkathoden-Technologie eingesetzt wird. Dieser Prozess führt zu einem um 30 Prozent niedrigeren Energieverbrauch bei der sonst sehr energieintensiven Chlorherstellung. Mit unserer Gasphasen-Technologie setzen wir auch bei der Herstellung des Schaumstoff-Vorprodukts TDI Maßstäbe Sie spart gegenüber konventionellen Prozessen Energie und Lösemittel, ist also einerseits nachhaltig, bietet andererseits aber auch einen klaren Wettbewerbsvorteil.
Wassernutzung
Allgemeine Informationen
Covestro verbrauchte im Jahr 2024 insgesamt 247 Millionen Kubikmeter Wasser, hauptsächlich aus Oberflächenwasser und von externen Lieferanten. Die nachhaltigen Betriebsabläufe des Unternehmens spiegeln sich unter anderem in seinem Wasserverbrauch wider, wobei 79 % als Durchlaufkühlwasser verwendet werden, das unverschmutzt an seine ursprüngliche Quelle zurückgeführt wird. 11 % des im Produktionsprozess verwendeten Wassers benötigten eine Behandlung, die verbleibenden Mengen konnten ohne weitere Behandlung entsorgt werden. Eine geringe Menge wird in der Produktion verbraucht.
Darüber hinaus hat das Unternehmen interne Recycling- und Wiederverwendungsprozesse, um den Wasserverbrauch in allen Abläufen zu optimieren. Im Jahr 2023 startete Covestro ein kontextbasiertes Wasserprogramm, das sich speziell auf Standorte konzentriert, die sich derzeit in wasserstressbelasteten Gebieten befinden oder in Zukunft befinden könnten, um das strategische Wassermanagement und die langfristige operationale Resilienz zu stärken. Mit nur 7 % der gesamten Wasserentnahme aus wasserstressbelasteten Gebieten bleibt die Risikoexposition begrenzt.
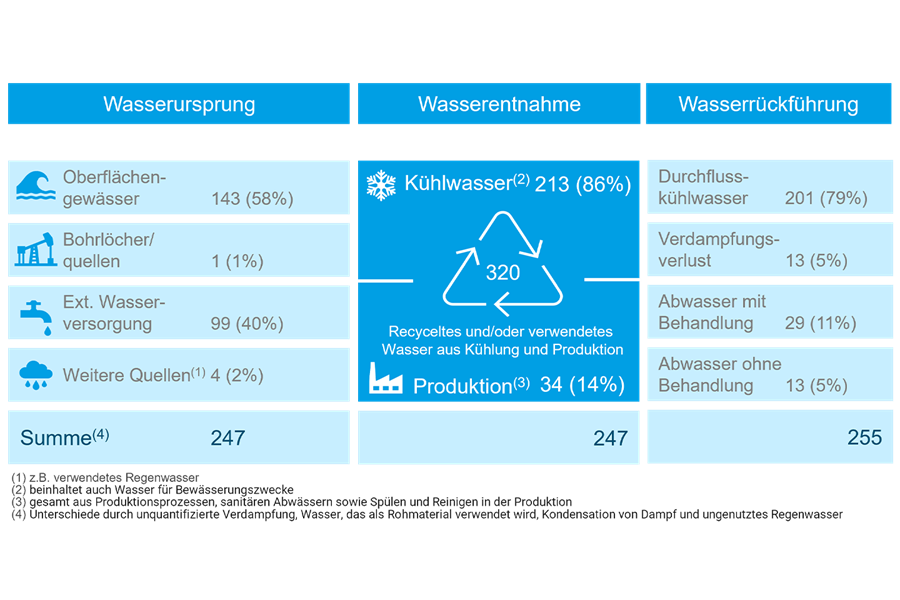
Wasseraufbereitung
Covestro versucht stets, gebrauchtes Wasser aufzubereiten und mehrmals wiederzuverwenden, wie etwa durch geschlossene Kühlwasserkreisläufe, die Wiederverwertung von aufbereitetem Abwasser oder die Rückführung von Dampfkondensaten als Prozesswasser. Im Jahr 2024 konnten so 320 Millionen Kubikmeter Wasser wiederverwertet werden. Der Großteil des von Covestro genutzten Wassers ist sogenanntes „Durchflusskühlwasser“, das ohne vorherigen Kontakt mit anderen Materialien oder Produkten aufgeheizt wird. Aus diesem Grund kann es – beinahe ausnahmslos – zur weiteren Aufbereitung wieder in den Wasserkreislauf eingespeist werden. Das produzierte Abwasser wird streng überwacht und geprüft, bevor es in den Abwasserkanal geleitet wird. In speziell darauf ausgelegten Aufbereitungsanlagen wird das Abwasser gereinigt, und erst danach wieder in den Wasserkreislauf eingespeist.
Im Januar 2016 nahm ein Pilotwerk zum Recycling von salzhaltigem Industrieabwasser den Betrieb am Standort Krefeld-Uerdingen auf. Das geschlossene Kreislaufsystem wird vom Bundesministerium für Umwelt, Naturschutz und nukleare Sicherheit (BMU) im Rahmen seines Umwelt-Innovationsprogramms gefördert und befindet sich aktuell in der technischen Probephase. Mithilfe des in Zusammenarbeit mit Covestro neu entwickelten Verfahrens soll die Chlor-Alkali-Elektrolyse mit bis zu mehreren 10.000 Tonnen weniger Salz und mehreren 100.000 Tonnen weniger vollentsalztem Wasser pro Jahr auskommen. Dies Entspricht Emissionseinsparungen von mehreren 1.000 Tonnen CO2-Äquivalent pro Jahr. Darüber hinaus kann dies die Menge an salzhaltigem Abwasser, das in den Rhein fließt, reduzieren.
Die Technologie bildet die Grundlage für das neue Gemeinschaftsprojekt „Re-Salt“ (Recycling von salzhaltigem industriellem Prozesswasser). Re-Salt hat eine geplante Laufzeit von drei Jahren und ein Budget von rund 3,4 Millionen Euro, wovon etwa 60 Prozent vom Bundesministerium für Bildung und Forschung (BMBF) bereitgestellt werden. Ein zentrales Ziel des Projekts ist, den Salzgehalt im Prozesswasser so zu regeln, dass dieses so umweltfreundlich wie möglich ist. Dies soll vor allem durch die Nutzung der Abwärme angrenzender Produktionswerke gelingen. Covestro plant ein Vorführungswerkwerk für Testzwecke am Standort Krefeld-Uerdingen.
Alternative Ressourcen
Fossile Ressourcen werden knapper und ihre Aufbereitung zur Verwendung in chemischen Produkten kann sehr energieintensiv sein. Wir möchten daher mehr und mehr alternative Rohstoffe verwenden. Auch wenn uns dies in verschiedenen Teilen unserer Produktion bereits gelungen ist, arbeiten wir kontinuierlich an weiteren Projekten. Das langfristige Ziel: Irgendwann womöglich ganz auf fossile Ressourcen verzichten zu können.
Zudem hat Covestro wichtige Fortschritte in der Nutzung pflanzenbasierter Rohmaterialien für die Polyurethanproduktion gemacht. Diese bergen das Potenzial, die Abhängigkeit von fossilen Ressourcen zu reduzieren und den CO2-Fußabdruck des Werkstoffs zu verbessern. Im Jahr 2017 haben wir erstmals im Rahmen eines kooperativen Projekts ein biobasiertes Härtemittel für Veredelungslacke im Automobilbereich eingesetzt. Ganze 70 Prozent des in dem Härtemittel enthaltenen Kohlenstoffs werden aus Biomasse gewonnen. Das biobasierte Härtemittel reduziert die Nutzung fossiler Ressourcen und geht mit einem erheblich verbesserten CO2-Fußabdruck einher als fossile Optionen. Das innovative Produkt wurde erfolgreich angewendet, beispielsweise bei einem Solarautorennen im Oktober 2017 in Australien unter extremen klimatischen Bedingungen.
Darüber hinaus konnten wir auf Laborebene die wichtige Basischemikalie Anilin gänzlich aus Biomasse herstellen. Bislang wurde Anilin weltweit ausschließlich mithilfe fossiler Ressourcen wie Erdöl hergestellt. Der nächste Schritt unserer Forschung besteht darin, die Produktion von biobasiertem Anilin zu erweitern, bis schließlich eine industrielle Produktion möglich ist. Anilin wird in der chemischen Industrie als Rohmaterial für diverse Produkte verwendet. Covestro nutzt die Chemikalie zur Herstellung eines Vorprodukts von Polyurethan-Dämmschaumstoffen.
Operation Clean Sweep®
Covestro hat sich auf globaler Ebene einem freiwilligen Produktverantwortungsprogramm mit dem Namen Operation Clean Sweep® (OCS) verschrieben. Das Programm zielt darauf ab, den Verlust von Kunststoffpellets, -flocken und -pulver in Produktions- und Verarbeitungsprozessen zu verhindern, damit letztlich kein Kunststoff mehr in die Wasserversorgung gelangen kann. Im Rahmen seiner Verpflichtung für OCS wertet Covestro seine Werke hinsichtlich eines potenziellen Pelletverlusts aus, implementiert ggf. Verbesserungsmaßnahmen und schult seine Mitarbeitenden zu dem Thema. Darüber hinaus werben wir in der Wertschöpfungskette um eine stärkere Beteiligung, gehen aktiv auf unserer Partner in unserer Lieferkette sowie Logistikanbieter und Kunden zu, um ihre Unterstützung für das Programm zu gewinnen.
OCS ist ein globales Programm, das von Branchenverbänden auf der ganzen Welt geleitet wird, darunter das American Chemistry Council und die Plastics Industry Association in den USA sowie PlasticsEurope in Europa.
Informationen zu dem Programm in Europa finden Sie hier, für andere Regionen hier.