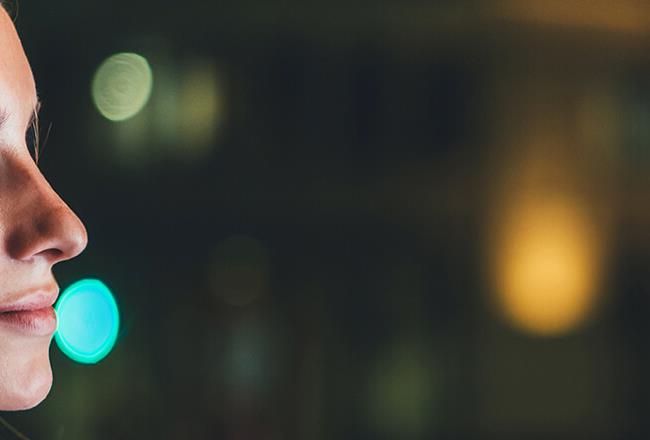
From random discovery to global success story
The future is circular: Present – 2015
Today, we are working on materializing our vision to become fully circular. We envision a world where all materials are reused instead of discarded. Innovations like our Evocycle® CQ technologies and materials that include a high amount of recycled resources and climate-neutral MDI are big steps towards our goal to achieve net-zero greenhouse gas emissions for us and our entire value chain by 2050.
Breaking new ground: 2014 – 2001
The start of the 21st century was our call to enter new territories of different kinds. We expanded to China and directed our efforts towards sustainability, reducing energy and emissions in production with inventions like ODC technology and STRUCTese®.
The story begins: 2000 – 1863
We started out as pioneering as we are today, by producing new coloring agents and with life-changing inventions, such as polyurethane foam and polycarbonates. It’s ideas like these that we owe our success to: in 1990, we would be the biggest supplier of raw materials for the rubber industry.