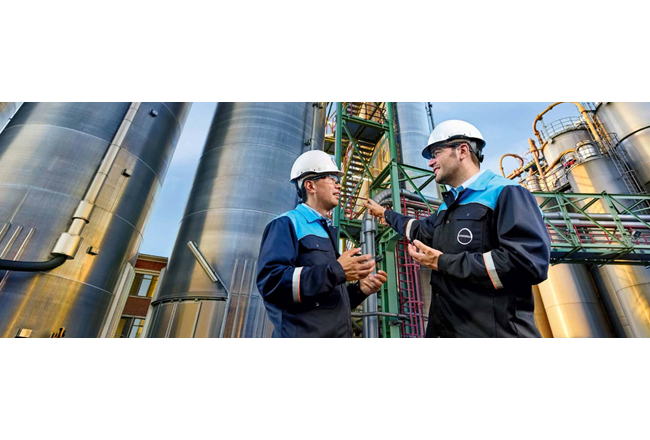
Sustainable Production: Visions for the Bigger Picture
Our Roadmap to Future Success
In a time where many companies are beginning to agree to follow sustainable practices, we at Covestro strive to be a leader of these practices. We aim to become a trailblazer for the use of alternative raw materials in our industry, constantly challenging the status quo and altering the concept of a company’s role in society. While we have a long track record in sustainability and are proud of all we have achieved, we work to push the limits of our own ambitions further. In 2022, we announced the ambitious target of being operational climate neutral by 2035, meaning reducing our Scope 1 and Scope 2 emissions to net zero. Powering our plants with renewable energy and implementing new technologies to further drive sustainability in our operations are just a few of the strategic measures we undertake to create a brighter future for our business and our planet.
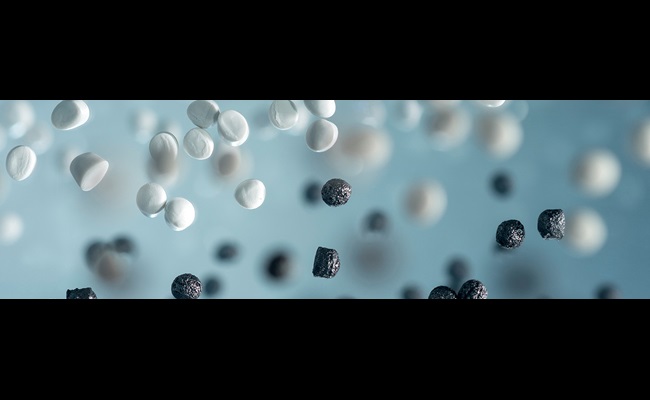
“The chemical industry needs large amounts of green electricity to make its contribution to climate neutrality and a truly sustainable future.“
Progress That Counts
Transitioning to clean energy is key to achieving sustainable development and meeting climate goals. That’s why we are proud to have signed the world’s largest corporate contract for offshore wind energy, giving green electricity a permanent place in our energy mix. With this agreement, we will cover a portion of our future electricity demand in Germany with wind energy from the North Sea.
Beginning 2025, energy supplier Ørsted will provide our German production sites with green electricity for a minimum of 10 years – an unprecedented step in emission reduction for the chemical industry in Europe.
More information
At Covestro, we strive to be a pioneer of the digital future because we recognize digital processes and data can help us reach our sustainability goals. Together with our partners and employees, we are actively seizing opportunities to drive digitalization in our research and development (R&D) as well as our operations.
By expanding our computer hardware and collaborating with industry leaders to create effective digitalization strategies, we are accelerating complex R&D processes and increasing computer simulation opportunities for test series. This digital focus not only helps us shorten time to market for innovative products, but it also makes developing products more sustainable by reducing material consumption and energy use.
An essential part of our digital transformation strategy is collaboration – not only within our company but also with strategic partners. In line with this approach, we have partnered with the CoPro project: an initiative that aims to "improve energy and resource efficiency by better coordination of production in the process industries.” Using online data analytics, computer-based control algorithms and other technologies, CoPro strives to provide tools for plant-wide optimization and balance production and consumption in industrial parks.
More information
Sustainable to the Core
Increasing Production Efficiency
Production processes in the chemical industry are resource and energy intensive. We continuously work to reduce emissions caused by our plants to a minimum, and decrease the dependency of fossil raw materials.
One way we achieve this goal is through our energy management system STRUCTese®. With it we monitor energy consumption at individual production locations and optimize energy usage, enabling us to potentially save more than 1.65 million megawatt hours annually. STRUCTese® is already being used at production sites all over the world.
Measures for more efficiency in production
Isocyanates and polyols are the two primary compounds used to make polyurethanes. As a world-leading supplier of both components, we have succeeded in making their production easier, more cost-effective, and more environmentally friendly than ever before. One milestone in this endeavor is gas-phase technology. As a result of this innovative technology, our production of isocyanate now uses far less resources than conventional, liquid-based processes.
This cleaner production process reduces solvents by around 80 percent and energy usage by around 60 percent. What’s more, annual carbon dioxide emissions for a typical large-scale plant (with a production capacity of 250,000 metric tons of TDI) are 60,000 metric tons lower than standard processes. We have been using gas-phase technology at our site in Shanghai since 2011 and at our Dormagen site since 2014.
Many industrial processes produce a substantial amount of wastewater with very high salt concentrations. That’s why we’re focused on finding economically viable methods for the treatment and re-use of this wastewater.
Together with industry partners and scientists, we have developed an eco-friendly way to recover salt and water from industrial wastewater: We call it “Re-Salt” technology. The water and salt recycled using Re-Salt can later be used to manufacture chlorine – a chemical that plays a central role in many of our production processes. In the future, our goal is to develop a wastewater treatment process that not only benefits plastic manufacturers but also provides other industries cleaner production opportunities.
Around 60 percent of all chemical products are made, directly or indirectly, using chlorine and/or sodium hydroxide. One of the major challenges facing the chlorine-alkali industry is the large amount of energy used by salt electrolysis in the creation of chlorine and sodium hydroxide. To tackle this problem, a team of Covestro chemists and engineers developed a groundbreaking process that produces chlorine more sustainably: Oxygen-depolarizedcathode (ODC) technology. When compared to traditional chlorine processes, ODC technology uses around a quarter less energy. For their boundary-pushing work, the creators of this ODC technology were awarded the Covestro Science Medal.
Moving into the future, we plan to introduce this breakthrough production technology into our plants, including a new chlorine production plant we are building in Tarragona, Spain. Once complete, our plant in Tarragona will be the first industrial-scale plant based solely on this state-of-the-art technology. The use of ODC technology is expected to not only increase the plant’s sustainability but also enhance the site’s competitiveness. About a third of the cost of manufacturing chlorine is typically spent on energy, so the technology will make an important economic impact.
More information
Press release on ODC plant in Tarragona
Press release on Covestro Science Medal
Sustainable Production
Using Alternative Materials
Preserving natural resources is a top priority for us. That’s why we’re constantly working on improvinga the energy efficiency and environmental compatibility of materials. Our primary aim is to help establish sustainable alternatives to fossil raw materials like crude oil and ensure innovative materials are produced in an eco-friendly manner.
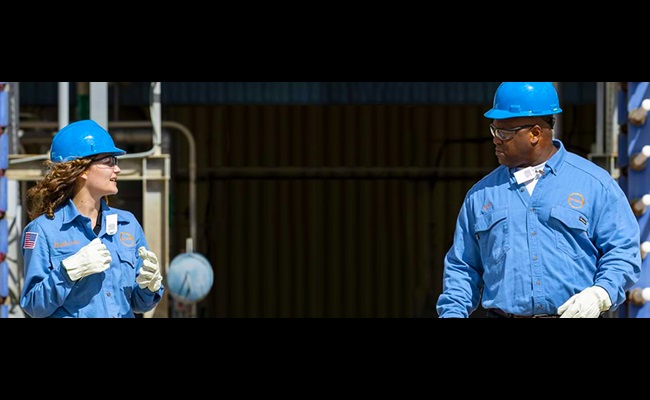
“Sustainability concerns society as a whole. That’s why Covestro teams up with partners in various industries to achieve true environmental breakthroughs.“
More Sustainability for Our Partners and Customers
Our dedication to sustainability doesn’t end at our factory gates. We put great emphasis on sustainability throughout the entire life cycle of our products and technologies. This commitment begins with our ambitious supplier management, which ensures the way we conduct business with our suppliers is in line with our environmental, social, and ethical standards.
Stories that push boundaries
Follow the links below and learn more about our commitment to make the world a brighter place.