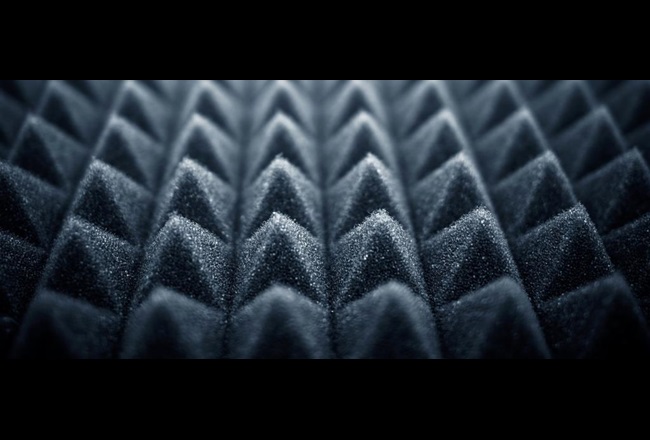
Materials for polyurethane foams
Materials for polyurethane foams
The new materials are revolutionizing the polymeric foam or polyurethane foam sector. Since their introduction on the market, which took place massively in the middle of the last century, polyurethane foams are now used in all sectors and industrial areas. The cellular structure of the foams absorbs or prevents exchanges of thermal or kinetic energy and therefore the foams are used as insulators and protection from shocks but also to make our life more comfortable by softening the surfaces intended for rest and sitting. The cellular structure and the quality of the bubbles are produced in the chemical process between materials that react with each other and give the foams their peculiar characteristics. Therefore the choice of polymeric materials and the technologies for the formation of the foam are the main variables to be taken into consideration in order to obtain structures with the thermal and mechanical characteristics necessary for the various fields of application.
Covestro's challenge in the field of foams is not only to supply polyurethanes with excellent physical / mechanical qualities but to support and research ever more performing technologies that are industrially scalable. Alongside materials that have been tested over the years, there are new material projects inspired by the creation of sustainable polyurethane foams that will implement a fully circular future that will make possible what today seems only a utopian vision.
Polyurethane foams: polyols and isocyanates
The chemistry of foamed polyurethanes sees as the main actors a poly oil that reacts with an isocyanate. Toluene diisocyanate (TDI) gives rise to flexible foams and diphenylmethane diisocyanate (MDI) is used for rigid foams. Additives of different nature are added to this mixture to affect the creation and quality of the cell structure.
The demand for polyurethane foams, due to their workability characteristics, ease of production and variety of application, is progressively increasing. It has been calculated that up to 2025 there will be an annual growth of 6%. Responding to market needs and improving the environmental impact is the programmatic horizon that Covestro has set for the next few years. Alongside the investment for the creation of new industrial sites, the improvement of the production technologies of the TDI and MDI isocyanates, compatible with the mission of sustainability and full economic circularity, was finalized. While a poly oil has been in production since 2016 that contains 20% of CO2 recovered from the production sites, making the polyurethane of soft foams more sustainable.
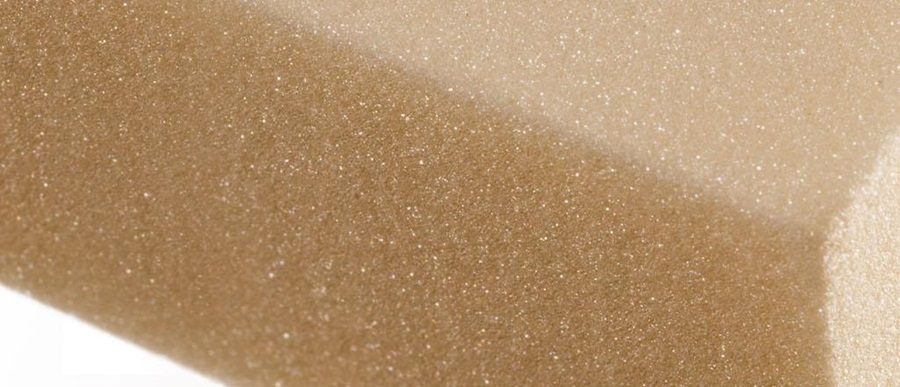
MDI and TDI for more sustainable polyurethane foams
Producing isocyanates in a green way is increasingly necessary to create sustainable polyurethanes. It is essential to identify which components in the production of MDI and TDI can be replaced by renewable or recycled substances. Covestro intends to use 60% of substances from secondary raw materials.
In the MDI Covestro has identified 5 elements that can be replaced with non-fossil materials, whose technologies already exist and are available for scale production.
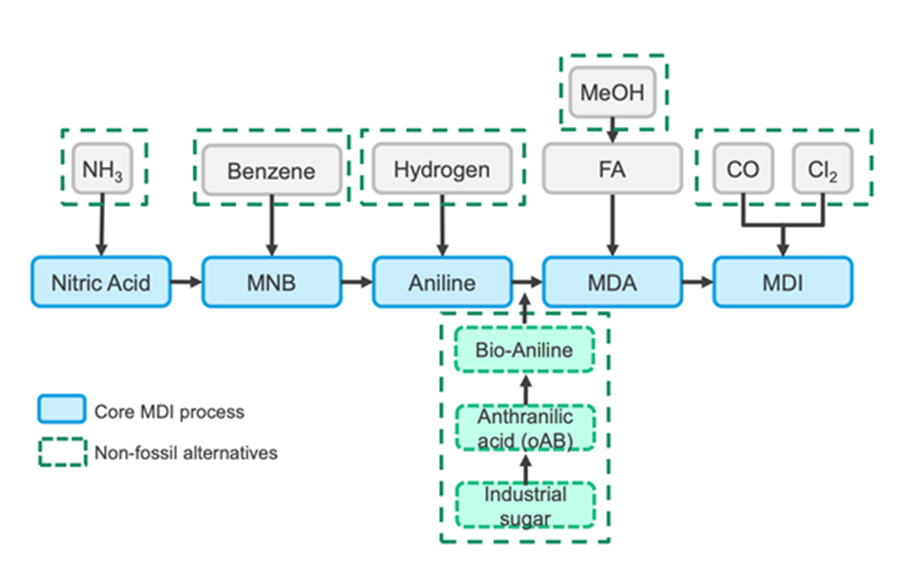
- Benzene from renewable biomass
- hydrogen (H2) from proven manufacturing processes using alkaline or water electrolysis
- ammonia (NH3) obtained from biomass
- methanol (MeOH) obtained by treating non-recyclable industrial waste
- carbon monoxide (CO) obtained from waste or from the combustion fumes of biogas.
Even a precursor, such as aniline, can be synthesized from renewable sources in the sugar transformation process.
In the production of the TDI, Covestro has identified the possible substitutions of fossil raw material with other more bio-compatible ones.
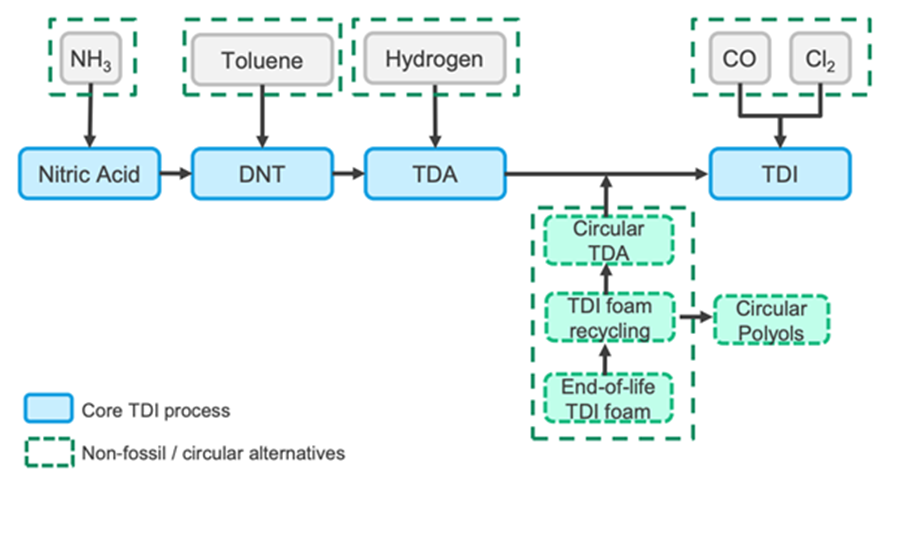
Polyols with recovery CO2
Since 2016 Covestro has begun to market a poly oil for polyurethane foams that uses recovered CO2 as a component from industrial waste. A new technology has been identified thanks to special catalysts developed with the CAT Catalytic Center of the University of Aachen, Germany. The advantages are on the one hand to recover industrial emissions that would otherwise be dispersed into the environment and, on the other hand, to have polyols for polyurethane foams with the same performance as traditional materials but with a greater green footprint.
Materials and systems for high performance polyurethane foams
The formulations of the foams provide for numerous combinations of precursors, polyols and isocyanates with the addition of additives such as water, catalysts or surfactants to obtain foams with different physical and chemical characteristics. A complex formulation work that allows industries to have tailor-made solutions based on specific requests. Covestro has in its catalog proven systems for flexible, rigid or spray foams suitable for every application need: from construction to automotive, from furniture to clothing. Numerous properties can be adjusted in each system with the selection of reactant materials to achieve specific requirements such as density, hardness and damping properties.
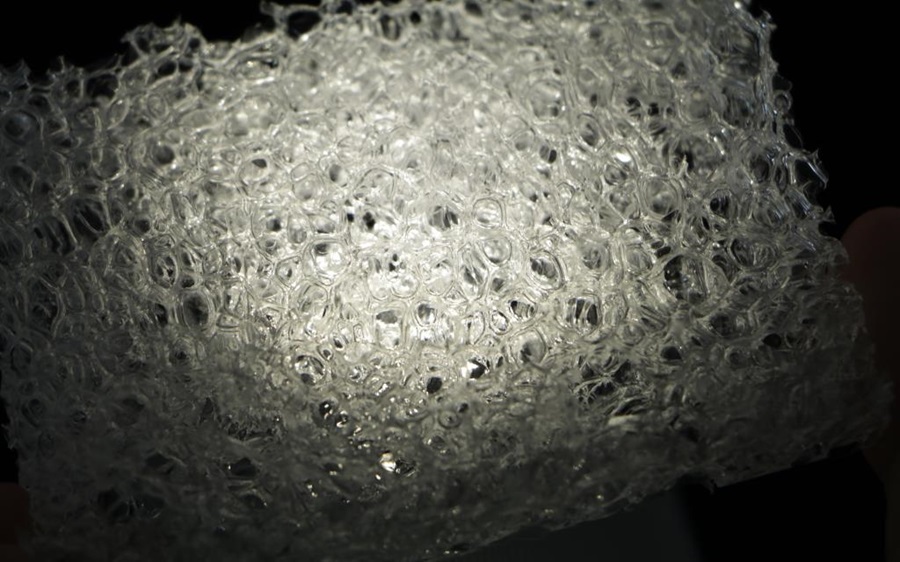
Flexible foam
Soft foam systems can be suitable for mold-in modeling or for the production of plates to be transformed by cutting.
Dispensing the liquid reaction mixture into a mold allows for high quality foam products with complex geometries for furniture, automobiles and other applications. Thanks to the numerous variables of the materials of the mixture, parameters such as insulation, sound absorption, impact resistance can be precisely calibrated.
Flexible plate foam is formed by pouring the liquid reaction mixture onto a laminator and a rectangular foam block is obtained. Most flexible foam blocks have a density between 15 and 60 kg / m³ and are used in the manufacture of mattresses or furniture. Different types of foam can be produced with this technology, such as conventional foam, high resilience (HR) foam, polyester based foam and viscoelastic foam.
Rigid foam
Inspired by thermoplastic injection molding, Covestro since the 1960s has designed and perfected the RIM (reaction injection molding) system for the production of polyurethanes using the two materials - isocyanate and polyol - in liquid form. With this system it is possible to obtain foam components with various degrees of flexibility but also extremely rigid depending on how the polyurethane system is formulated. The technology works with feed lines that dose materials at high pressure and with a mixing device. The liquid is then injected into a closed mold where the chemical reaction takes place and a polyurethane polymer is formed. Cycle times vary according to the size of the piece and the polyurethane system used. For an average mold, demoulding can take place in 30-60 seconds, with an interesting production scalability for industries.
Continuous rigid foam sheets can be used in composite panels that serve as insulation in buildings. The rigid PU foam core can be obtained by joining sheet metal to metal composite panels or by applying flexible coatings to insulation panels in so-called double belt conveyors (DBC).
Spray foam
In the case of cavities to be insulated, surfaces to be reinforced or for molding processes, spray technology is used. Covestro has in its portfolio materials for customizable spray foam systems. The reactive liquid mixture comes out of the spray gun to be applied in the desired places. As with other PU-based technologies, it is possible to vary the stiffness of the foam from flexible to rigid by dosing the quantity and quality of the precursor materials and additives.