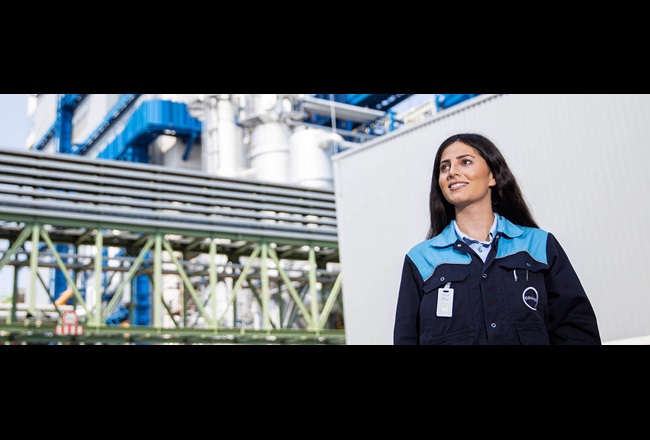
Covestro is committed to sustainable production
Covestro operates around 48 production sites in Europe, Asia, and the USA. The global orientation is the foundation for the company's success. However, the materials manufacturer has its roots in Germany, where more than 7,250 employees work. At its six sites in Leverkusen, Dormagen, Krefeld-Uerdingen, Brunsbüttel, Meppen und Bomlitz, materials are produced for important branches of industry – for example, for the automotive and construction industries as well as for the electrical and electronics industry.
Covestro has a broad base in Germany: Its production sites have both smaller plants for regional purposes and world-scale plants that serve the needs of global customers efficiently and reliably. Covestro always keeps a close eye on the technological optimization of its plants and processes: Here, quality, efficiency, and safety in production are given top priority.
Keeping climate-neutral production in sight
With its sustainable technologies and processes, Covestro aims to become operationally climate-neutral by 2035 and achieve net-zero emissions from its own production (Scope 1) and from purchased energy (Scope 2) by then. Some of Covestro's lighthouse projects show that the company is well on the way to reducing its Scope 1 emissions (see slider “Low energy consumption, lower greenhouse gas emissions”). Upstream and downstream greenhouse gas emissions in the value chain (Scope 3) are also to be significantly reduced by 2035 – in the long term, Covestro aims to achieve climate neutrality for Scope 3 emissions by 2050.
The innovative technology is used for the production of methylene diphenyl diisocyanate (MDI). Adiabatic isothermal phosgenation (AdiP) is characterized by more efficient reaction control and no need for external heat supply. Instead, it uses the heat generated during the reaction.
- Brunsbüttel
- Up to 40 percent less steam and up to 25 percent less electricity per metric ton of MDI produced
- This corresponds to a reduction in energy-related CO₂ emissions of around 35 percent
By setting up an internal steam network, waste heat from the methylenediphenyl diisocyanate (MDI) plant can be used in the neighboring methylenediphenyldiamine (MDA) plant to treat wastewater. As a result, the chemicals needed to produce polyurethane foams are produced in a more energy-efficient manner.
- Krefeld-Uerdingen
- Reduction of carbon dioxide (CO₂) emissions in MDA operations by around 10 percent
Variable frequency drives were installed on the cooling water circulation pumps in a polycarbonate plant to optimize pump pressure and control.
- Krefeld-Uerdingen
- Reduction of energy consumption by 700 megawatt hours per year
By integrating heat – i.e. cross-linking processes that need to be cooled with those that need to be heated – the waste heat generated in toluene diamine (TDA) operations can be put to use in the neighboring toluene diisocyanate (TDI) system. In the form of slack steam, it is used to operate an evaporator and two absorption chillers. This significantly reduces the amount of steam that has to be sourced from the site’s power plant.
- Dormagen
- CO₂ emissions were reducted by 28 percent for operation of TDI plant
In 2014, a large-scale toluene diisocyanate (TDI) plant with a production capacity of 300,000 metric tons per year was put into operation. It was modernized between summer 2023 and March 2025. As a result, the raw material TDI required for the production of soft plastic is produced in a particularly resource-efficient manner. Gas phase technology is also used in the production of coating raw materials at the Leverkusen hexamethylene diisocyanate (HDI) plant. This can reduce energy and solvent consumption.
- Dormagen (TDI plant), Leverkusen (HDI plant)
- Savings of 80 percent solvents, up to 80 percent energy
In the nitric acid production plant, an innovative catalyst is used for exhaust gas cleaning.
- Dormagen
- Reduction of emissions of climate-damaging nitrous oxide by 95 percent
In a chlor-alkali electrolysis with oxygen depolarized cathodes, chlorine and caustic soda are obtained from common salt and water. The process reduces oxygen as a reaction partner and avoids the formation of hydrogen, thereby reducing electricity consumption and the associated CO2 emissions.
- Krefeld-Uerdingen
- Energy savings of up to 25 percent
Energy efficiency – a lever for greater sustainability
More energy-efficient production reduces climate-damaging CO₂ emissions and thus makes a contribution to the fight against climate change. Covestro is therefore constantly working to improve energy efficiency in its production facilities. For example, Covestro uses STRUCTese®, a self-developed energy management system, across the Group to optimize production processes and increase energy efficiency. The actual energy consumption in production is compared with the realistically possible optimum. STRUCTese® includes many different stages of analysis, monitoring, and benchmarking. Eliminating inefficiencies results in permanent energy savings.
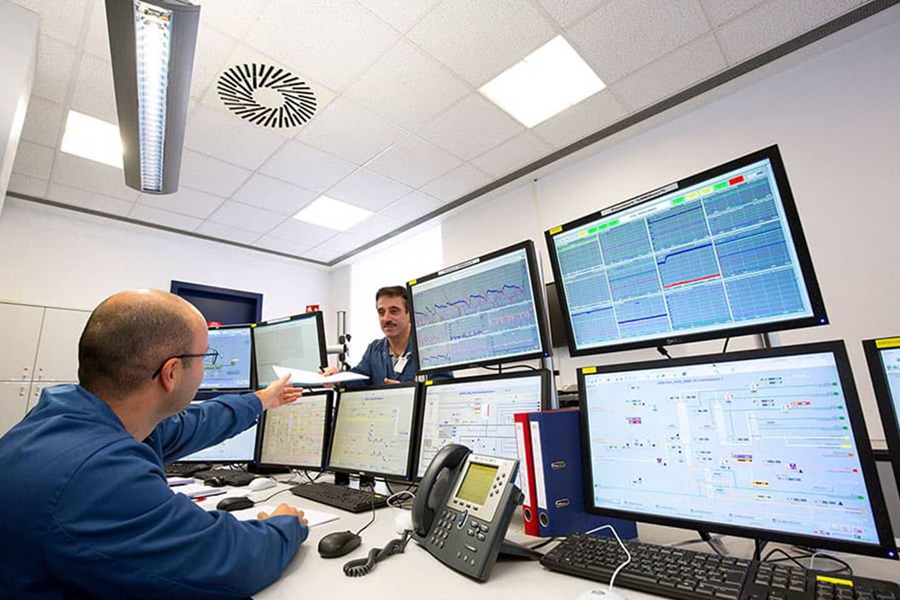
A broad product portfolio – also in Germany
Covestro manufactures an extensive range of products for its core business at its six German sites. It consists of of two segments: "Solutions and Specialties" and "Performance Materials". The company is expanding its capacity based on market demand. In order to unlock further synergies in production and at the same time cut costs, Covestro also established a site network in North Rhine-Westphalia in 2010. It includes the plants in Leverkusen, Dormagen, and Krefeld-Uerdingen.
The circular economy as a new guiding principle
Covestro also intends to transition its production in Germany to the circular economy. In order to become fully circular, the materials manufacturer has set up a long-term strategic program. In future, raw materials from sustainable sources such as waste and biomass are to be used in the manufacture of innovative products to the greatest extent possible. This further reduces dependence on fossil resources such as oil. This has a positive effect on climate protection. With its program, Covestro wants to become a shaping force in the chemical and plastics industry.
Used plastics in particular play a crucial role in the upcoming transformation. Waste and used materials are valuable resources and should be recycled systematically and as far as possible. Covestro intends to develop new technologies exactly for this purpose. With the circular economy, the company can contribute to a climate-neutral and more resource-efficient economy and society just like its customers. In North Rhine-Westphalia, Covestro already uses a number of innovative processes that illustrate the company´s circular approach.
However, circular economy is only truly sustainable if green power is used. Covestro has already set the course for this at its German sites. The increased use of digital technologies also ensures even greater efficiency in production. An excerpt from the projects in Germany can be found here:
Climate-neutral by 2035: that is Covestro's ambitious goal. On its way to a "greener" future, the company has already made some landmark decisions. In the future, Covestro intends to cover a significant part of its electricity requirements in Germany with wind energy from the North Sea. For this purpose, Covestro signed the world’s largest industrial customer supply contract for electricity from offshore wind turbines with Ørsted at the end of 2019.
Starting in 2025, the Danish energy supplier will provide Covestro with green electricity for ten years, which will come from a newly constructed wind farm off the German North Sea island of Borkum. The agreement covers a capacity of 100 megawatts - enough to supply 300,000 people with electricity.
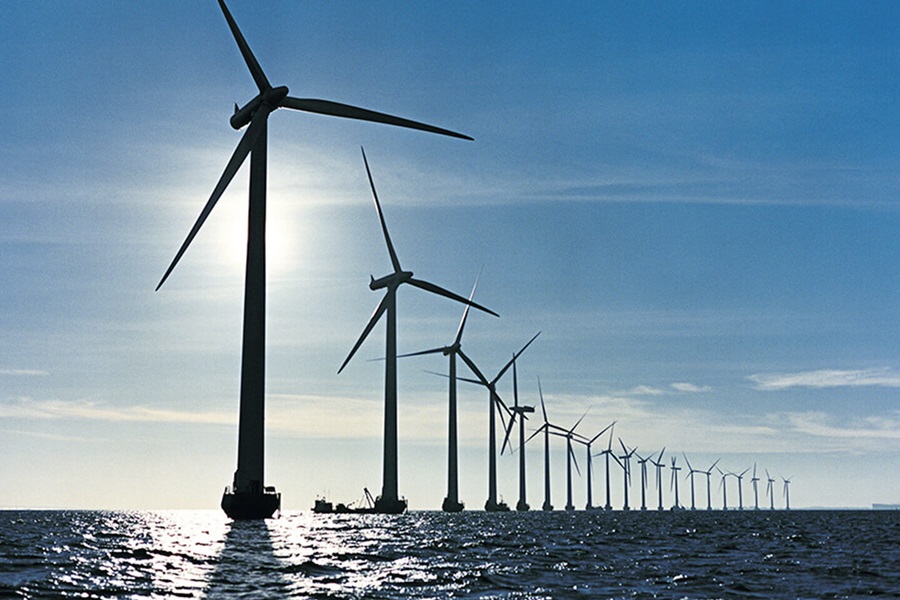
Covestro has also signed a Corporate Power Purchase Agreement (PPA) for solar power with the energy company EnBW. Since 2022, the material manufacturer has thus secured 63 megawatts of EnBW's "Weesow-Willmersdorf" solar park in Brandenburg. The contract is intended to run for an initial period of 15 years. Covestro plans to primarily use the solar power for the production of sustainable, mass-balanced plastics manufactured using the drop-in process at the sites in Dormagen and Krefeld-Uerdingen.
The 465.000 solar modules of the park have been fully connected to the grid since March 2021 and produce a total of 187 megawatts of power. The agreement with Covestro is the project's first industrial customer supply contract.
In 2023, Covestro in Germany already obtained 17 percent of its energy from renewable sources. In the long term, the company aims to rely entirely on a climate-friendly energy supply.
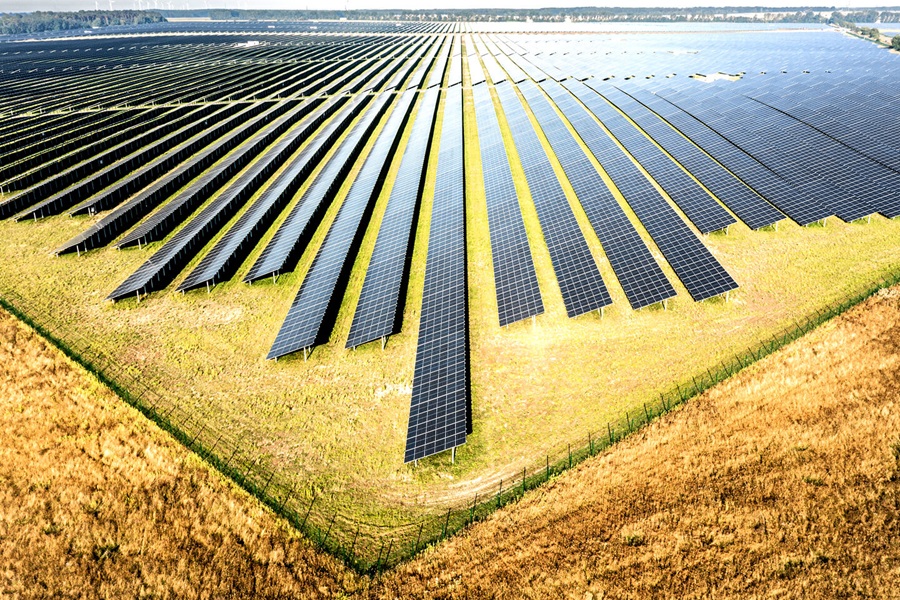
Making production more sustainable – this is also possible thanks to advancing digitalization. It opens up entirely new opportunities to make processes more efficient. Covestro has been driving digitalization forward in core areas of the company for many years. In this way, Covestro generates competitive advantages through cost efficiency and differentiation. Products and processes are becoming even more efficient and sustainable with data analysis, new digital applications, and simulation and blockchain technologies, for example, in production and research and development.
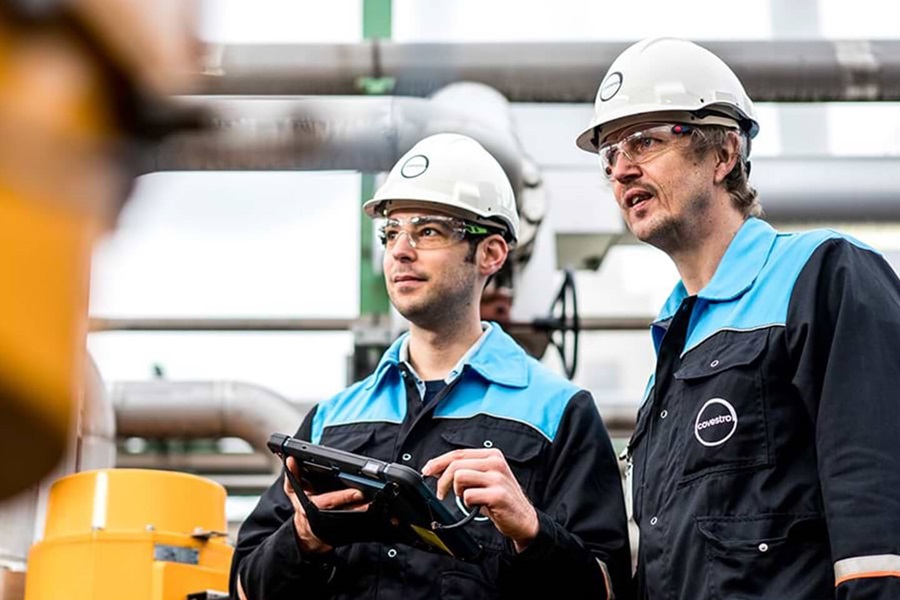
Digital technologies are already ensuring that Covestro sets new standards. They help make material cycles even more efficient.
The company is also further expanding “mobile maintenance” – i.e. plant maintenance using mobile devices. This not only allows work steps to be reduced, but also further improves processes in the production facilities. Maintenance measures can also be planned and structured more efficiently, resulting in increased planned runtime and reduced costs. The new process is currently being used in Krefeld-Uerdingen among other places. It is soon to be deployed at other German sites.