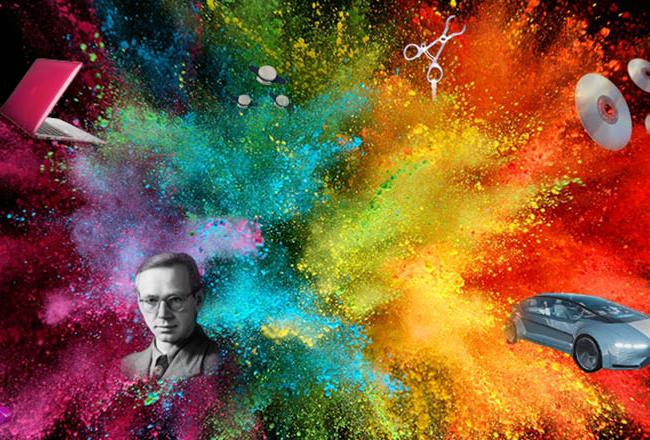
70 years of polycarbonate
Schnell patented his revolutionary invention that same year. The certificate dates back to October 16, 1953. What Schnell could not have foreseen at the time: Under the brand name Makrolon®, the polycarbonate was to enrich the lives of millions of people around the world in the decades to come - and the success story is not likely to come to an end soon. The Covestro site in Krefeld-Uerdingen plays a decisive role in this story to this day.
„Shatterproof, resistant and easy to process - polycarbonate has numerous exceptional properties and has become an indispensable part of our everyday lives. And the future also looks promising: With the climate-neutral* Makrolon® RE grades, we are taking another big step toward a circular economy.“
Even though polycarbonate is now produced at various sites around the world - it is and remains a Krefeld original. But what makes the Covestro material so special? Its outstanding qualities! Makrolon® is robust, lightweight and transparent. In addition, it is easy to process. Plus, the material retains its original size in changing environmental conditions - for example, at very high or low temperatures.
At the same time, polycarbonate also excels in terms of its aesthetic benefits. This is because Makrolon® can be supplied in a variety of colors and can be used in a wide range of applications. It is particularly suitable for designing appealing surfaces - and thus helps Covestro customers to set completely new trends. All this makes Makrolon® so popular with manufacturers of automotive parts, sports equipment, electronics, eyewear, medical devices and many other products.
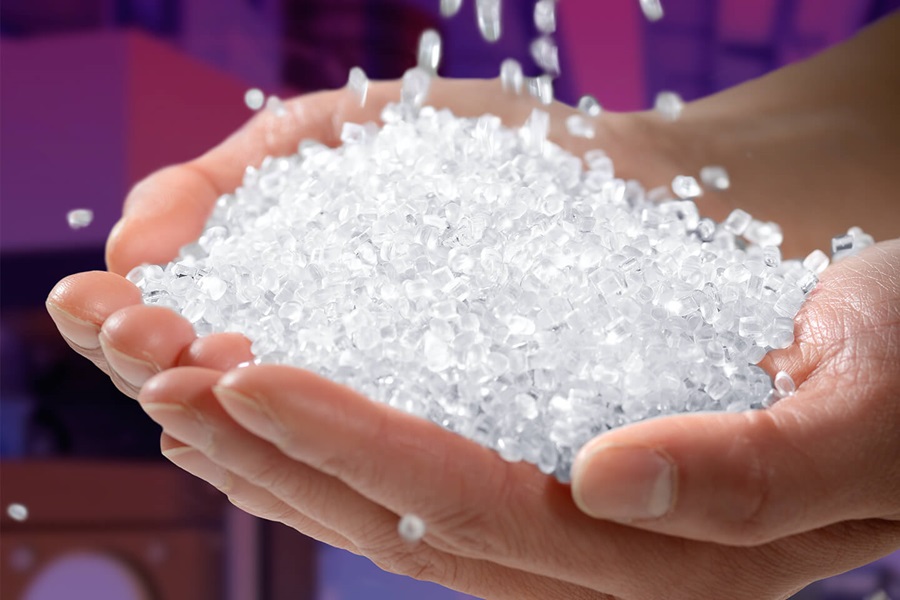
Material with many talents
Meanwhile, Makrolon® is opening the door to more and more innovations. In the automotive industry, for instance, the Covestro material enables greater design freedom on the way to electromobility. Many manufacturers have therefore relied on the company's material solutions for years. Both the BMW iX and the Ford Mustang Mach E GT already roam the roads with polycarbonate parts.
The medical technology sector is also making steady progress thanks to Makrolon®. The material plays an indispensable role in the development of diagnostic equipment in particular. Thanks to its biocompatibility and sterilizability, it can be used without difficulty in devices for monitoring and treating diabetes, for example. According to a study by the University of Washington, an estimated 1.3 billion people worldwide will suffer from the chronic disease in 2050 - more than twice as many as today. To make life easier for patients with diabetes, healthcare companies are working on making wearable devices for continuous blood glucose monitoring increasingly smaller. This is precisely made possible by the flexible applications of Makrolon®.
Polycarbonate paves the way to climate neutrality
In 2021, Covestro celebrated an important milestone in Krefeld-Uerdingen: the delivery of the world's first climate-neutral* polycarbonate. It is manufactured using electricity from renewable sources and raw materials derived from mass-balanced biowaste and residual materials. For Covestro, this is an important milestone in the transition of its product portfolio to alternative raw materials. The climate-neutral* Makrolon® RE grades are the material of choice for customers looking for alternative raw materials with a lower carbon footprint. The products offer the same quality and performance as fossil-based polycarbonates. Plus, they can be processed in exactly the same way - existing processes and workflows can remain exactly the same.
Covestro is also continuing to make important progress in the recycling of materials. In addition to mechanical recycling, which is already an important component of Covestro's recycling strategy, the company is continuously developing chemical recycling. Chemical recycling works in a complementary way to mechanical recycling - it converts plastic components back into monomers, which are their individual components. These can be separated and serve as raw materials for future plastics. In particular, chemical recycling can make larger waste streams that are unsuitable for mechanical processes accessible for recycling; it allows the production of plastics that meet the highest quality requirements. Technical implementation of this process on a pilot scale has recently started in Leverkusen.
Impressions
From Orbit to Olympia - the history of Makrolon®
In the recent history of mankind, polycarbonate has certainly found its place - as Makrolon® and sometimes also by other names. A little more than ten years after its discovery, the material was even used in space for the first time. A joint venture in the United States produced the versatile material at the time as a licensed product under the name Merlon. It proved to be a superior material for space research. Polycarbonate was used in the helmet visor of astronaut Edward H. White, who made the second ever spacewalk on June 3, 1965, floating freely in space for about 21 minutes.
Almost 40 years later, Makrolon® set a record at the Olympic Games in Athens. During the opening ceremony in the summer of 2004, guests were able to marvel not only at the many athletes but also at the world's largest stadium roof made of the material. A full 25,000 square meters - equivalent to around 3.5 soccer fields - of the highly transparent and solid plastic panels were used in the construction. An architectural masterpiece! The following timeline shows the historical milestones in which the innovative Makrolon® was involved.
* The “climate-neutral” rating is the result of an assessment of a section of the entire product life cycle. The section from resource extraction (cradle) to the factory gate was considered. The assessment is based on ISO standard 14040 and was critically reviewed for plausibility by TÜV Rheinland. The assessment considers biogenic carbon sequestration based on preliminary data from the supply chain and the use of renewable electricity in the production process. The allocation of electricity was based on so-called "Guarantee of Origin" certificates. So-called offset certificates were not applied.