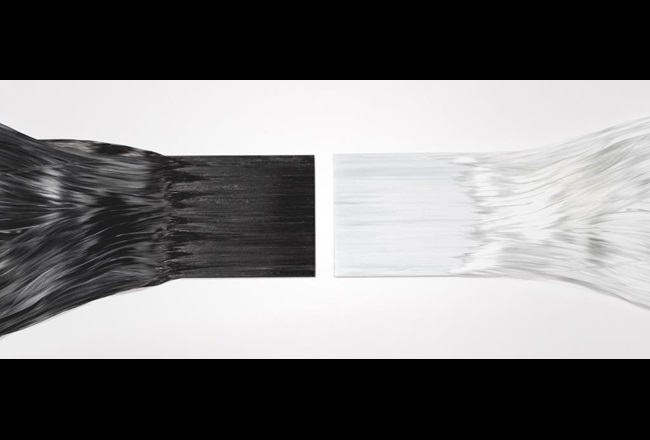
Materials for composites
Polymeric materials for composites
More and more performing, economical and suitable composites for scale productions are obtained thanks to the new polymeric materials for the matrices. From the thermosetting resins of the first glass fiber, carbon or aramid fiber composites, we are moving towards the adoption of polyurethane-based thermoplastic materials. New materials are asked to solve specific problems of a project or to create products that require less energy in their production and transformation into semi-finished products. Having advanced composite materials also allows us to face the important challenges of energy and environmental sustainability related to the production and end-of-life phases of composite materials.
The cost of a component made of composite material depends on the manufacturing processes and can reach 75% of the total costs. This represents a major obstacle to the growth and use of composites in various applications. Specifically, the problems are related to the deposition process, treatment times and certification aspects. Most of the studies are aimed at solving these problems and concern:
- process innovations
- new functional materials
- development of advanced software tools
- extension of collaborations with equipment manufacturers (OEMs) and certification authorities.
Covestro's collaboration with companies for the solution of specific problems and production challenges has led to new solutions for composites, both with products ready to be used on a scale, and with the definition of innovative mixtures and processes.
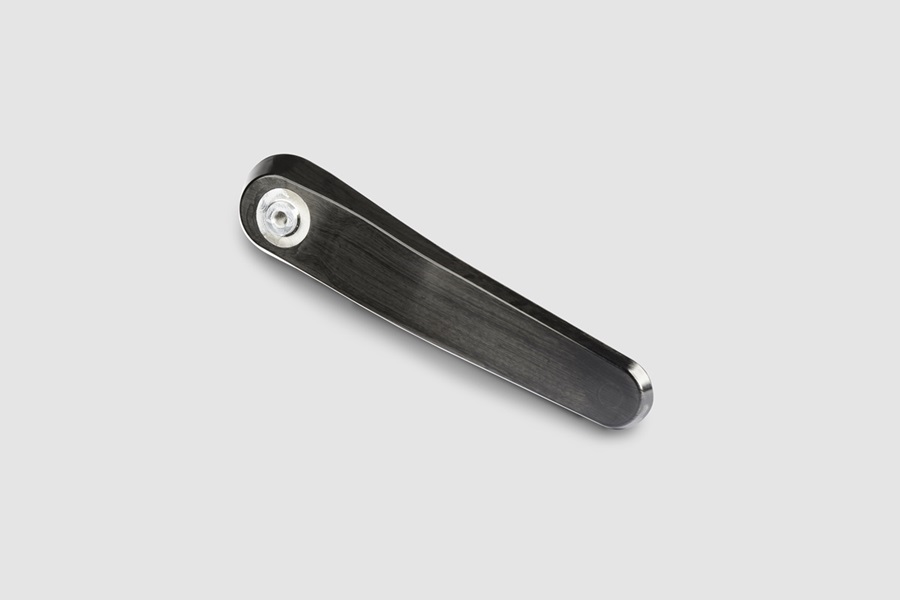
Aliphatic polyurethane for outdoor composites
One of the problems with outdoor composites is the resistance of the polymer matrix to UV rays. Many outdoor applications, especially if they have large surfaces, use aluminum, steel, wood or concrete. Composites that are stable and resistant to ultraviolet radiation involve complex, expensive and uncompetitive machining. Covestro tested a material with a thermosetting matrix based on aliphatic isocyanates, characterized by unique performances on the market. The aliphatic polyurethane developed by the Covestro laboratories protects the composites from degradation due to environmental effects, such as sunlight or brackish climates. UV stabilizers or protective coatings are no longer required. Alongside these properties, chemical resistance, scratch resistance and certified flame retardancy have been tested. The single component PU system is easy to process with standard equipment and does not require investment in new machinery. Like the whole family of polyurethanes, it has a high reactivity and cross-linking speed combined with an adjustable viscosity and the ability to incorporate the reinforcing fibers in a homogeneous way.
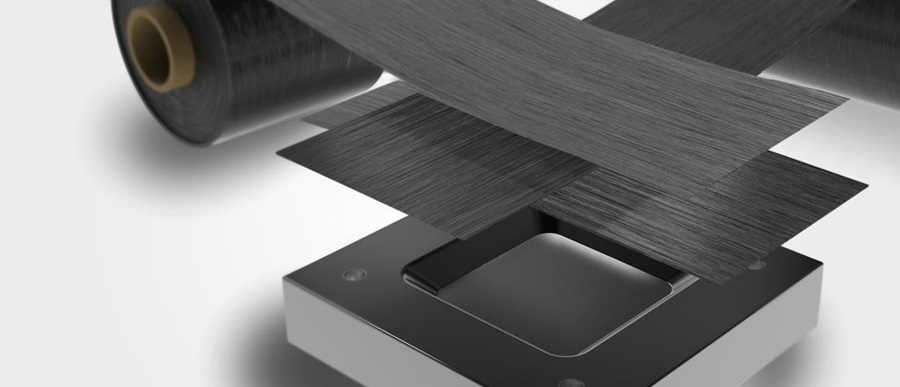
Aliphatic polyurethane for composites in the vacuum infusion process
The vacuum infusion method (VIP) is gaining momentum among the production methods of composite materials. The low cost, the production speed and the final perfection of the pieces made, is making it a very used method in various industrial sectors. In the VIP, the introduction of the resin matrix no longer takes place by injection but through a depression created by a pump that draws the resin itself onto the mold on which the reinforcing fibers are arranged. In this method it is essential that the matrices are resins with precise characteristics for an optimal final result. Covestro has in its portfolio of high-tech mono and two-component polyurethane resins that have low viscosity characteristics and short curing times. They are perfect for the VIP infusion process as well as for the autoclave infusion (HP-RTM) process. The high reactivity of the polyurethane system ensures a fast and complete reticulation (snap cure) so that the finished piece can be extracted from the mold after a short time. It has been tested that the production cycle is around a few minutes, which makes it convenient to adopt this method in industries that require fast times such as automotive and transport in general. The high-tech polyurethane resins have also been tested with regard to two fundamental parameters for the automotive sector:
- absorption of kinetic energy three times higher than other resins and greater protection in the event of an accident
- lightness of the composite components which translates into lower vehicle weight and consequent reduction of CO2 emissions.
Covestro has also developed solutions with composites that can be structured in sheets with a honeycomb structure, extremely resistant and light. By adding a central layer of polyurethane foam, insulating sandwiches with superior mechanical and physical characteristics are obtained, perfect for the automotive or aerospace industry.
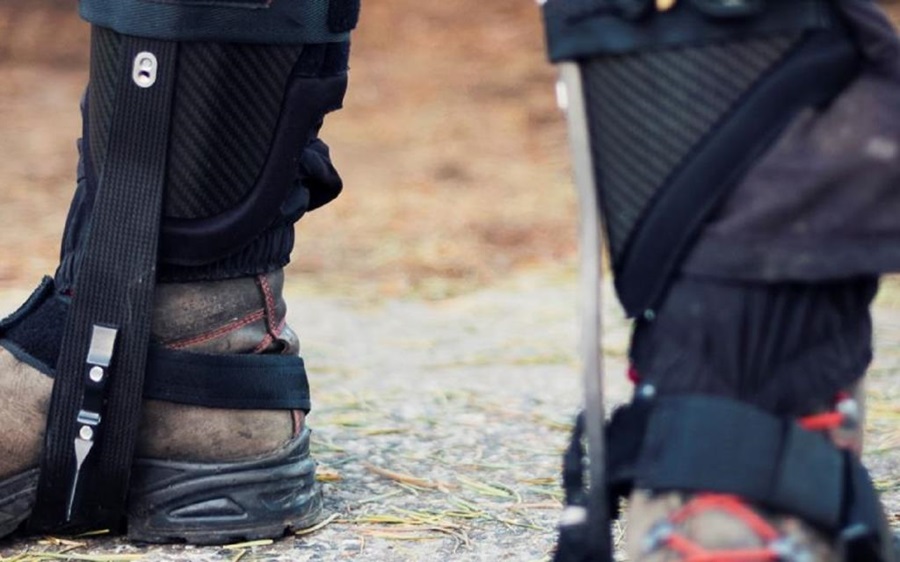
Aliphatic polyurethane for composites for pultrusion
Pultrusion allows to produce composite material products quickly, automatically and with a high production volume. The production process in which the resin-impregnated fibers are pulled into a heated mold has in fact the advantage of totally excluding the manual component and thus of obtaining components in a continuous way ready for use. The matrix of these composites is usually unsaturated polyester resin. Covestro, on the other hand, offers a low viscosity polyurethane resin specific for pultrusion. Reinforced with carbon fiber, the composites obtained are profiled with structural characteristics of solidity and resistance equal to steel but with a considerably lower weight than metals. The profiles have been used in various application fields. Carbon fiber automotive chassis have a lower tare weight and transport companies can move goods with heavier loads and thus operate more efficiently. In e-mobility, the lightweight frame compensates for the weight of the battery and at the same time offers easier assembly and greater resistance in the event of an accident. In construction, carbon profiles have been used to construct structures for ventilated roofs, which have a low weight and optimal load behavior, resistance to atmospheric agents and less maintenance. Even the frames can be made with composite profiles combining superior structural characteristics that reduce the thermal transmittance (UF) values of doors and windows.
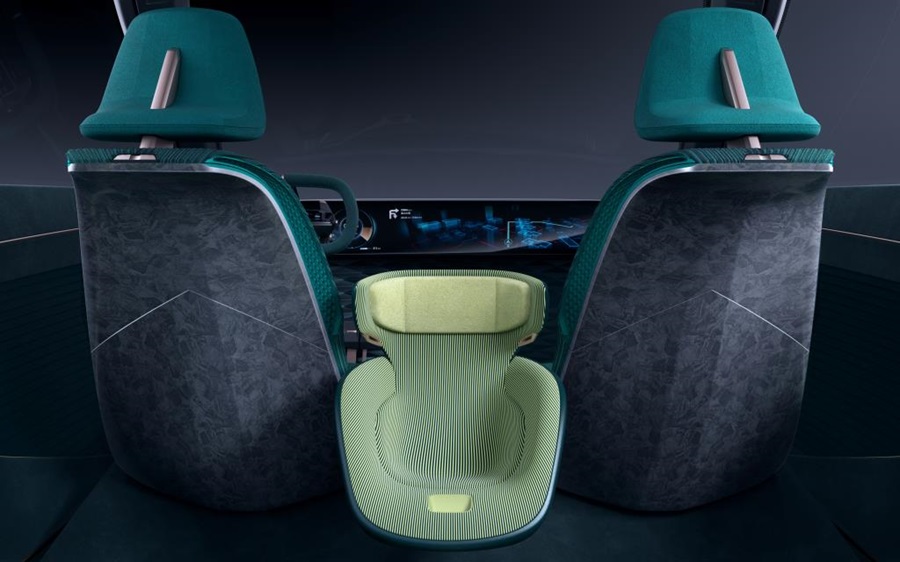
Materials for thermoforming or injection presses
The search for extremely performing composites has led Covestro to define a material in strips and sheets based on thermoplastic polyurethane resin reinforced by unidirectional carbon fibers. It is therefore ready for use and can be positioned in the molds according to structural and production needs even automatically. It is particularly suitable for making composite components with thermoforming, or with injection presses (hybrid molding). The possibility of automating some stages of the process, such as the positioning of fibers and ribbons, makes this technology also suitable for mass production. Being made of thermoplastic resin, this composite material is recyclable at the end of its life. Given the spread of composites in large product sectors, Covestro wanted to create a high-end material that combines strength, lightness and finish with versatility of use. From the more structural products for automotive and transport, to electricity and electronics, this composite has also found application for footwear, sports and leisure and consumer products for its many advantages:
- light and strong: has higher specific stiffness and strength than magnesium and aluminum
- infinitely adjustable: the direction of the fiber in each layer of the ribbon lamination can be adapted to meet specific performance goals
- Elegant finishes: the material has the touch and sounds like metals
- Easy to process: Thermoplastic composites enable thermoforming at high yield rates and short cycle times
- recyclable: can be recycled and reformed at the end of its life.