
Materiali per compositi
Materiali polimerici per compositi
Compositi sempre più performanti, economici e adatti a produzioni di scala si ottengono grazie ai nuovi materiali polimerici per le matrici. Dalle resine termoindurenti dei primi compositi in fibra di vetro, in carbonio o in fibre aramidiche, si sta passando all'adozione di materiali termoplastici a base poliuretanica. Ai nuovi materiali si chiede di risolvere specifiche problematiche di un progetto o di realizzare prodotti che richiedono meno energia nella loro produzione e trasformazione in semilavorati. Avere materiali compositi avanzati permette di affrontare anche le importanti sfide della sostenibilità energetica e ambientale legate alle fasi di produzione e fine vita dei materiali compositi. Il costo di un componente realizzato con materiale composito dipende dai processi di produzione e può raggiungere il 75% dei costi totali. Ciò rappresenta un grande ostacolo alla crescita e all’utilizzo dei compositi nelle diverse applicazioni. Nello specifico, le problematiche sono legate al processo di deposizione, ai tempi di cura e agli aspetti di certificazione. La maggior parte degli studi sono finalizzati alla soluzione di queste problematiche e riguardano:
- innovazioni di processo
- nuovi materiali funzionali
- sviluppo di strumenti software avanzati
- estensione delle collaborazioni ai produttori delle attrezzature (OEM) e alle autorità di certificazione.
La collaborazione di Covestro con aziende per la soluzione di problemi specifici e di sfide produttive, ha portato a nuove soluzioni per compositi, sia con prodotti già pronti per essere utilizzati su scala, sia con la definizione di miscele e processi innovativi.
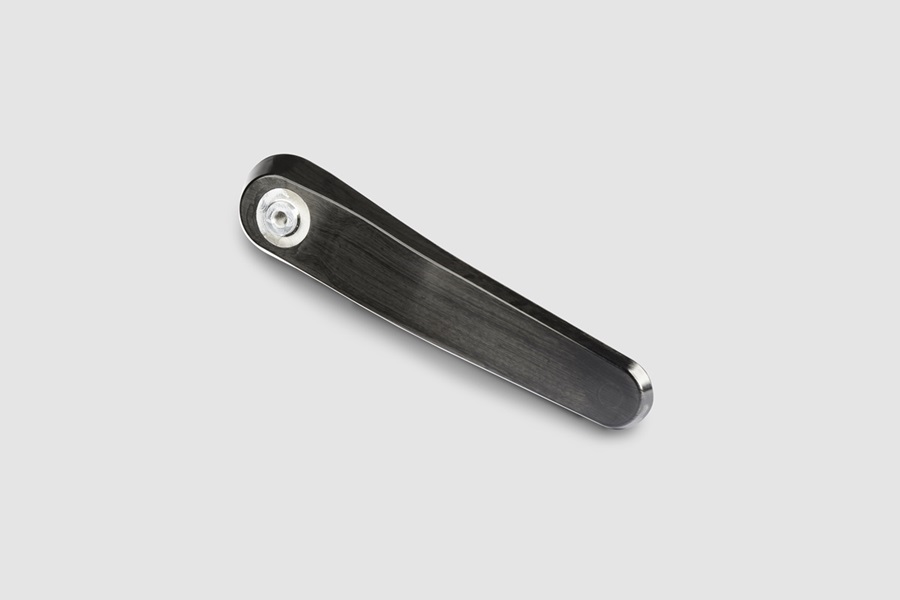
Poliuretano alifatico per compositi in outdoor
Uno dei problemi dei compositi in esterno è la resistenza della matrice polimerica ai raggi UV. Molte applicazioni per esterni soprattutto se hanno grandi superfici, usano alluminio, acciaio, legno o cemento. Compositi che siano stabili e resistenti alle radiazioni ultraviolette implicano lavorazioni complesse, costose e non competitive. In Covestro è stato testato un materiale con matrice termoindurente a base di isocianati alifatici, caratterizzati da prestazioni uniche sul mercato. Il poliuretano alifatico messo a punto dai laboratori Covestro protegge i compositi dalla degradazione dovuta agli effetti ambientali, come la luce solare o i climi salmastri. Non sono più necessari stabilizzanti UV o coating protettivi. Accanto a queste proprietà sono state testate la resistenza agli agenti chimici, le capacità antigraffio e un ritardo di fiamma certificato. Il sistema di PU monocomponente ha una facile lavorazione con attrezzature standard e non richiede investimenti in nuovi macchinari. Come tutta la famiglia dei poliuretani ha una elevata reattività e velocità di reticolazione unita alla viscosità regolabile e la capacità di incorporare in modo omogeneo le fibre di rinforzo.
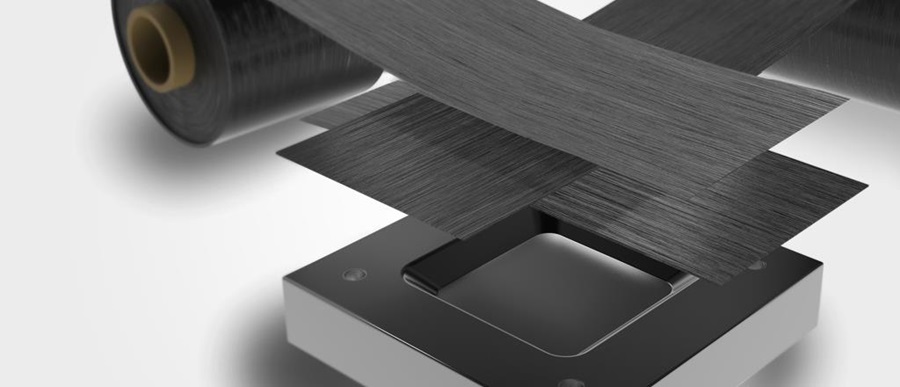
Poliuretano alifatico per compositi nel processo di infusione a vuoto
Tra i metodi di produzione dei materiali compositi si sta affermando il metodo di infusione a vuoto (VIP). Il basso costo, la velocità di produzione e la perfezione finale dei pezzi realizzati, la sta rendendo una metodologia molto usata in svariati settori industriali. Nel VIP l’introduzione della matrice di resina non avviene più per iniezione ma tramite una depressione creata da una pompa che richiama la resina stessa sullo stampo su cui sono disposte le fibre di rinforzo. In questo metodo è indispensabile che le matrici siano resine dalle caratteristiche precise per un risultato finale ottimale. Covestro ha nel suo portfolio delle resine poliuretaniche ad alta tecnologia mono e bicomponenti che presentano caratteristiche di bassa viscosità e di tempi di reticolazione brevi. Sono perfette per il processo ad infusione VIP come per quello ad infusione in autoclave (HP-RTM).
L'elevata reattività del sistema poliuretanico assicura una reticolazione veloce e completa (snap cure) così che il pezzo può essere estratto già rifinito dallo stampo dopo poco tempo. È stato testato che il ciclo di produzione si attesta intorno a qualche minuto, che rende conveniente l'adozione di questo metodo in industrie che richiedono tempi veloci come l'automotive e i trasporti in genere. Le resine poliuretaniche ad alta tecnologia sono state testate anche per quanto riguarda due parametri fondamentali per l'automotive:
- assorbimento dell'energia cinetica tre volte superiore rispetto ad altre resine e maggior protezione in caso di incidente
- leggerezza dei componenti in composito che si traduce in minor peso del veicolo e conseguente riduzione delle emissioni di CO2.
Covestro ha anche messo a punto soluzioni con compositi che si possono strutturare in fogli con struttura a nido d'ape, estremamente resistenti e leggeri. Con l'aggiunta di uno strato centrale in poliuretano espanso, si ottengono sandwich isolanti dalle caratteristiche meccaniche e fisiche superiori, perfette per l'industria automobilistica o aerospaziale.
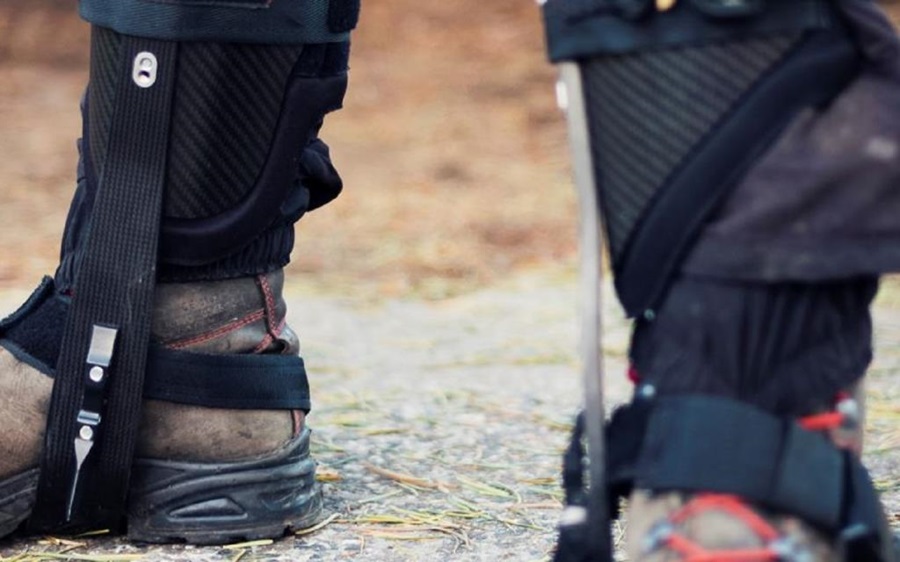
Poliuretano alifatico per compositi per la poltrusione
La poltrusione permette di realizzare prodotti in materiale composito in modo veloce, automatico e ad alto volume produttivo. Il processo di produzione nel quale le fibre impregnate di resina vengono tirate in uno stampo riscaldato, ha infatti il vantaggio di escludere totalmente la componente manuale quindi di ottenere componenti in modo continuo già pronti all'uso. La matrice di questi compositi è di solito in resina poliestere insatura. Covestro invece propone una resina poliuretanica a bassa viscosità specifica per la poltrusione. Rinforzata con fibra di carbonio, i compositi ottenuti sono profilati dalle caratteristiche strutturali dalla solidità e resistenza pari all'acciaio ma con un peso considerevolmente minore rispetto ai metalli. I profilati sono stati impiegati in diversi campi applicativi. I telai di autoveicoli in fibra di carbonio hanno una tara minore e le aziende di trasporto possono movimentare merci con carichi maggiori e quindi operare in modo più efficiente. Nella mobilità elettrica, il telaio leggero compensa il peso della batteria e allo stesso tempo offre un montaggio più semplice e maggiore resistenza in caso di incidente. In edilizia i profilati in carbonio sono stati usati per costruire strutture per tetti ventilati, che hanno un peso ridotto e un comportamento ottimale ai carichi, resistenza agli agenti atmosferici e minore manutenzione. Anche gli infissi possono essere realizzati con profilati in composito unendo caratteristiche strutturali superiori che riducono i valori di trasmittanza termica (UF) di porte e finestre.
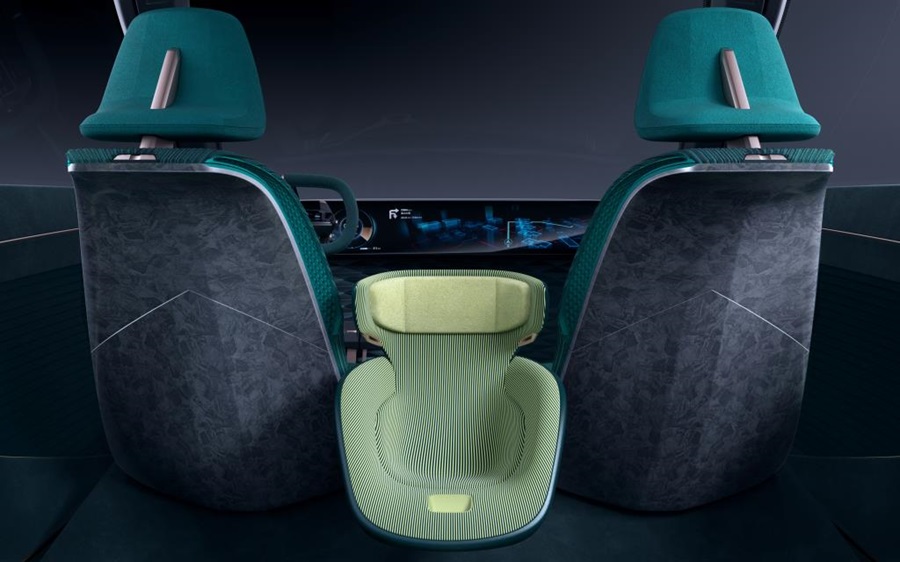
Materiali per termoformatura o presse a iniezione
La ricerca di compositi estremamente performanti ha portato Covestro a definire un materiale in nastri e in fogli a base di resina di poliuretano termoplastica rinforzato da fibre di carbonio unidirezionale. È così già pronto all'uso e può essere posizionato negli stampi secondo i bisogni strutturali e produttivi anche in modo automatico. È particolarmente indicato per realizzare componenti in composito con termoformatura, oppure con presse ad iniezione (stampaggio ibrido). La possibilità di automatizzare alcune fasi del processo, come il posizionamento delle fibre e dei nastri, rende questa tecnologia idonea anche a produzioni in grande serie. Essendo in resina termoplastica, questo materiale per compositi è riciclabile a fine vita. Vista la diffusione dei compositi in ampi settori merceologici, Covestro ha voluto creare un materiale di alta gamma che unisce resistenza, leggerezza e finitura a una versatilità d'utilizzo. Dai prodotti più strutturali per automotive e trasporti, fino all'elettricità ed elettronica, questo composito ha trovato applicazione anche per calzature, sport e tempo libero e prodotti di consumo per i suoi numerosi vantaggi:
- leggero e resistente: ha una rigidità e una resistenza specifiche più elevate rispetto al magnesio e all'alluminio
- regolabile all'infinito: la direzione della fibra in ogni strato della laminazione del nastro può essere adattata per soddisfare obiettivi prestazionali specifici
- finiture eleganti: il materiale ha il tocco e suona come i metalli
- facile da lavorare: i compositi termoplastici consentono la termoformatura ad alti tassi di resa e tempi di ciclo brevi
- riciclabile: può essere riciclato e riformato a fine vita.