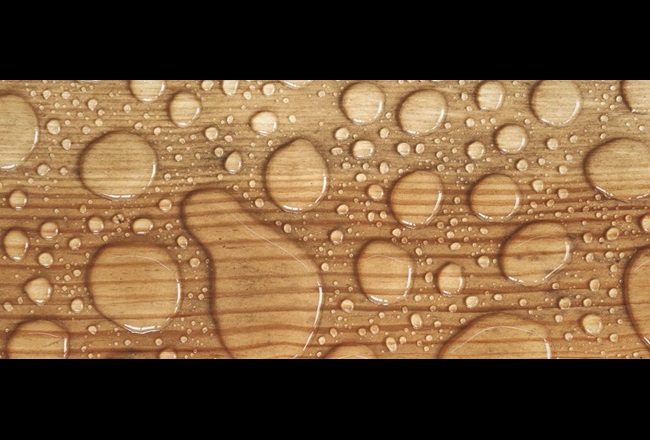
Coating or coating materials
Polymeric materials for coating
The task of coatings is to cover the surfaces of a product with suitable materials to protect it from external agents or to improve its physical characteristics. The coating materials can be liquid, paste or powder which transform into a sealing film and give the object the desired mechanical and chemical protection.
The broad spectrum of performance that is desired from a coating implies that there is not a single type of material that satisfies so many requests. The goal of obtaining coatings with lasting protection at reasonable prices can only be achieved by adopting different formulations based on a remarkable range and combinations of materials. Each of these combinations can give rise to extremely specialized coatings with optimal application techniques and specific chemical / physical properties.
Covestro experts collaborate with companies in all sectors to identify the most suitable polymer formulations for the different market needs, the materials they must adhere to and the stresses they must resist. A wide portfolio of raw materials is available to coating producers and users: resins, dispersions and binders, combined with the correct application technologies.
Raw materials, formulations and application methods for high quality coatings
The resins, with their film-forming capacity, constitute the main material of the coatings. They are then mixed with additives, solvents and pigments to obtain products for protective coatings. If the film-forming agents are liquid materials with low molecular weight, it is also possible to eliminate all or part of the solvents. When resins or dispersions are miscible with water, the solvents can be replaced by water.
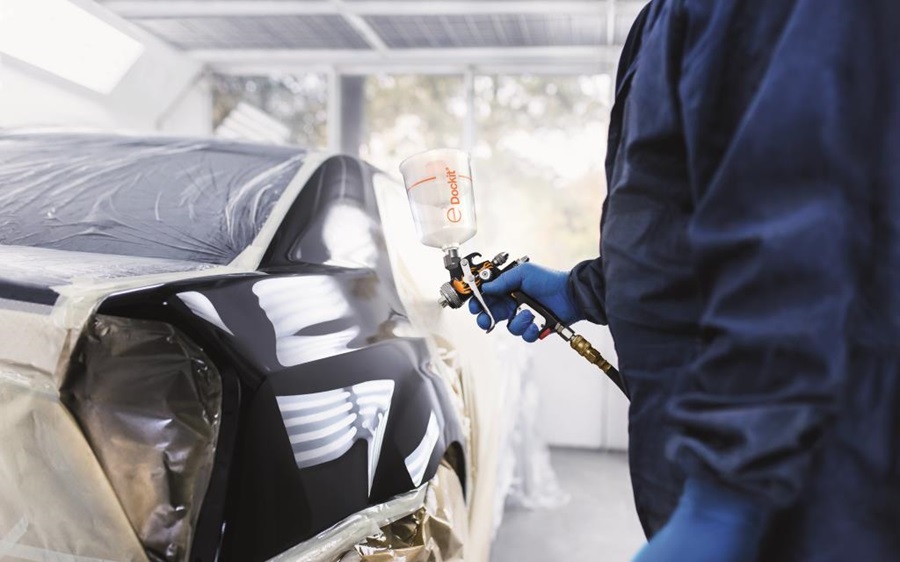
Polymeric resins for coating
The coatings are divided into two basic groups. In the former there are physically cured film-forming agents with higher molecular weight, such as cellulose nitrate, cellulose acetobutyrate, thermoplastic acrylates and also PVC copolymers. These resins are fixed by releasing solvents, but do not undergo a chemical change during the formation of the film.
The second group includes chemically reactive film-forming agents and are used for high quality decorative and industrial coatings. The crosslinking reaction can be initiated by heat or catalysts. These are enamels based on acrylic-amino resins, alkyd-amino resins or combinations of phenolic resins that dry at high temperatures. Alkyd resins have an oxidative polymerization, i.e. in air, and crosslink more slowly at room temperature. Polyurethane paints and epoxy resins polymerize very quickly even at room temperature and, due to their high chemical reactivity, are supplied in 2 components.
Research has shifted the focus on particle morphology, size and interaction associated with surfaces, leading to nanotechnology.
Solvents and pigments in coatings
Solvents are an essential component in coatings, in addition to determining viscosity and ease of use, they can affect the final yield and obtain perfectly level surfaces. Reactive solvents are also being used which have fewer emissions. The pigments are very important, because they not only have an aesthetic function but, if they are of high quality, they can improve the capabilities of the coating with respect to resistance to UV rays and corrosion.
Covestro has been able to obtain high quality coatings, paints and coatings thanks to the wide catalog of polymeric raw materials: hardeners, resins, dispersions and binders, combined with continuous research and collaborations with producers in every sector.
State-of-the-art solutions with high resistance to scratches, corrosion and atmospheric agents, both solvent-based and water-based. Among the leading products are polymers produced with CO2 from biomass, more sustainable and which respond to the principles of the circular economy that inspires Covestro's founding values.
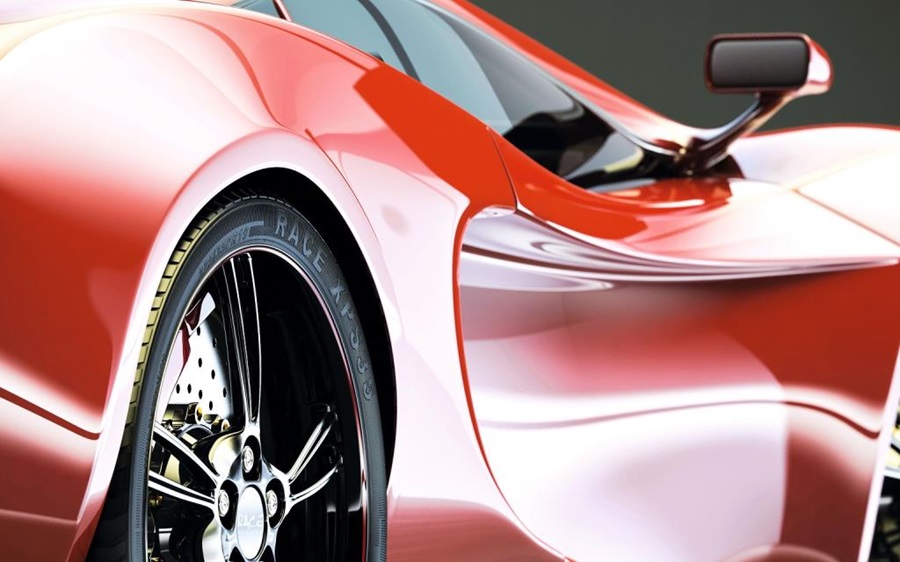
Mixtures of polyisocyanates for coating in the automotive sector
Car manufacturers are asking for coatings that make painting more efficient and faster. Covestro has experimented with car manufacturers a polyisocyanate-based polyurethane coating (clear, two-component, solvent-based) for metal and plastic. In synergy with a catalyst it improves the crosslinking process during the drying phase and accelerates the hardening times with the heat of the ovens by lowering the temperature from 140 ° C to just 90 ° C. The result is a uniform, smooth, resistant paint with low energy consumption and reduced processing times.
Lowering the drying temperatures and shortening cooking times also means a decrease in carbon emissions. While the faster times allow a cost saving which has been calculated by 6% compared to traditional methods, without investments in new infrastructures or compromises in the quality of the surfaces obtained. This coating contributes to pursuing quality and sustainability in the automotive sector.
Polyurethane dispersions in building construction
Giving great performance without facing high costs. This is one of the most important challenges facing public and private construction. Infrastructure and housing must be economically sustainable, durable and resilient to atmospheric aggressions. Covestro responds to this demand with self-crosslinking acrylic dispersions (PAC) and polyurethane dispersions (PUD). These are eco-sustainable and biocompatible water-based resins, which allow versatile, economical and high-performance coatings for construction products.
Polyurethane materials can be used in variable mixtures depending on their
- versatility: they adhere to multiple substrates and have varying degrees of flexibility
- ease of use: one-component and two-component formulations
- fast drying: self-crosslinking dispersions have short drying times
- durability: high chemical and abrasion resistance
- economic sustainability: same performance as high-end coatings
- low environmental impact: the aqueous base has fewer emissions and odors.
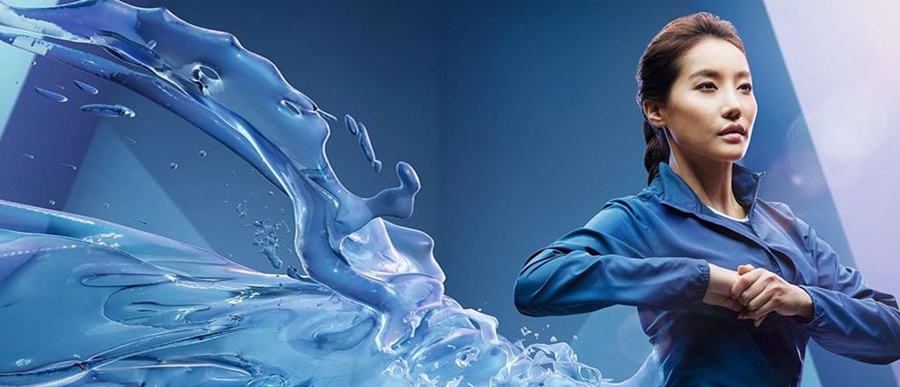
Polyaspartic resins in flooring and waterproofing
Particularly important is the sector of coatings for waterproofing and treatment of indoor or outdoor surfaces subjected to strong mechanical stress and the most demanding atmospheric agents. Covestro has pioneered a one-component polyaspartic coating that has found wide applications: from business vehicles, to private construction to public facilities such as hospitals and bridges. Tested for over 15 years of use, the technology tested in the Covestro laboratories has made it possible to reduce the layers, passing from the traditional three to only one or at most 2 coats of painting, with savings in terms of labor and material to be used. Curing times for this material are also reduced by up to eight times and ISO 12944 standards are met for corrosion resistance and durability.
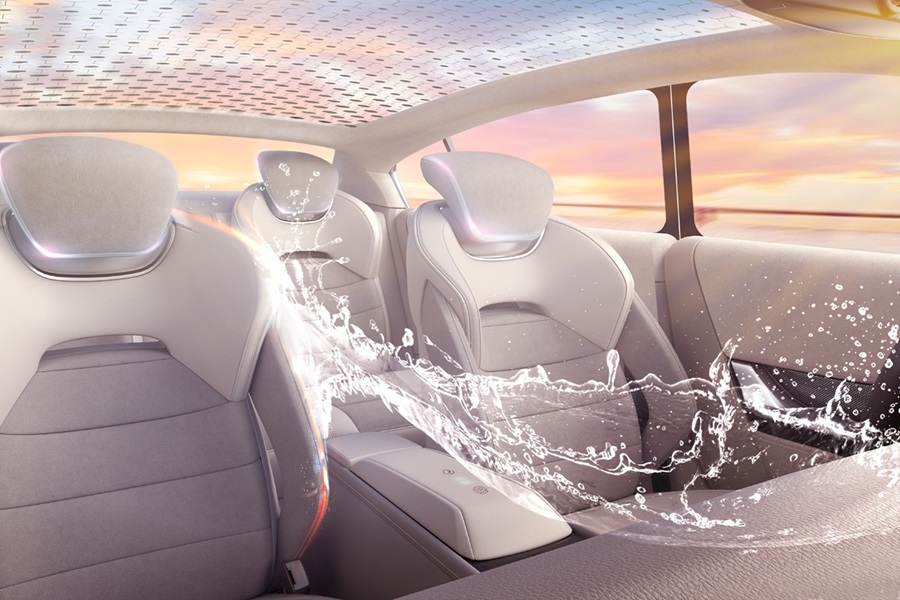
Direct Coating: the new frontier of coating
The novelty in terms of coating is the polyurethane coating integrated into the automotive components such as dashboards, spoilers and control panels with controls already in the molding phase. With technology that has now been tested for scale production, Covestro has found a way to combine the injection molding of thermoplastics and the reaction injection molding (RIM) of PU systems in one process. A thermoplastic support is created in the mold and then transferred to a second zone which is enlarged by the thickness of the coating layer. In this space, the PU system is then injected onto the support. The integration of the film in the component brings numerous advantages: production time, perception of the final piece and absence of waste or risk of overspray.