Polymeric materials for adhesives and sealants
It's hard to imagine a product in your home, industry, transportation, or anywhere else that doesn't use adhesives in some way. Today the adhesive market is valued at $ 7473.37 million and is expected to reach $ 10982.38 million by 2028.
It is an extremely varied product sector in which technologies and materials are constantly evolving to offer the best solutions from the point of view of tightness, cohesion, resistance to external or atmospheric agents.
There are four main classes of raw materials used in adhesives:
- vinyl
- acrylics
- natural or synthetic rubbers
- polyurethane.
And a whole series of polymers are emerging that find application in specific sectors.
Raw materials and formulations create an infinite range of adhesives and sealants
The combination of polymers adopted and chemical formulation make the adhesives almost tailor-made for specific requests and uses.
Water-based systems currently represent more than 50% of European demand for adhesives. The main applications can be found in packaging and construction. Another type is solvent-based, mainly used in contact adhesives in construction or in clothing to assemble materials such as leather or synthetic fabrics. This technology is subject to stringent regulations and a lower perception of value by consumers.
Other highly requested formulations are reactive systems because they create a structural adhesive bond with the materials to be joined. They can be one-component or two-component as in epoxy adhesives.
A growing technology is that of so-called hot melt adhesives or hot glue. Its versatility, resistance to water and humidity, and low cost make it the ideal choice in many applications and are replacing solvent-based adhesives. Ultimately it is understood how adhesives can be composed of many polymeric raw materials and additives from natural or synthetic sources. Every slightest variation of the formulation will give adhesives that will behave differently both in the polymerization mechanisms and in the mechanical and physical characteristics over time.
Covestro has a large catalog of raw materials and base polymers, from the most proven to high performance materials for advanced applications. The company has been working for some time alongside the industries of the various sectors to provide the most suitable, safe and performing formulations based on the needs of the end user. And in this field the possibilities for innovation seem to be endless.
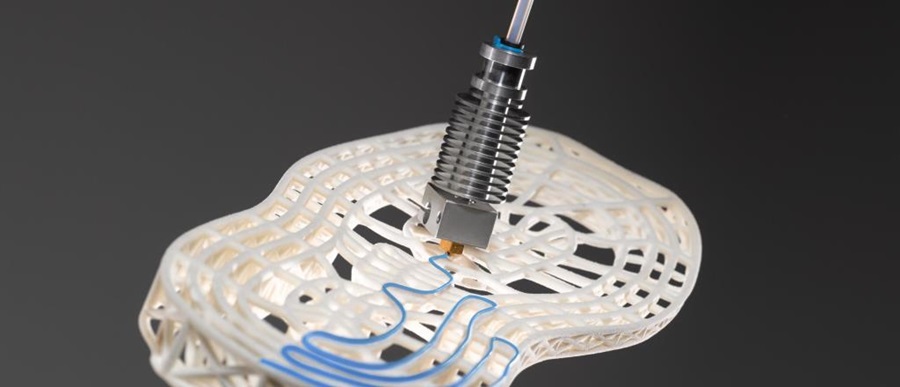
Materials for solvent-based adhesives
With combinations of polyols and polyisocyanates, solvent-based two-component adhesive systems are obtained. Infinite degrees of possible mixing, which vary according to the molecular characteristics of both the polyols and the polyisocyanates used. This type of adhesives has good wetting properties, especially on solvent permeable substrates, thus achieving great bond strengths. Due to their thermoplastic nature, solvent-based adhesives have a limited resistance to deformation when exposed to the action of heat, on the other hand they are sensitive to solvents and tend to deform permanently when subjected to loads. In the industrial field, these adhesives are mainly used in the furniture, footwear, automotive and construction industries for cold welding PVC pipes.
Some Covestro adhesive materials have a history of over 70 years, therefore they are proven products and highly appreciated by the markets. Polyols can be in liquid form or in granules characterized by low viscosities which make them better for application. Two-component adhesives offer particularly high strength and resistance and are ideal for bonding and laminating in furniture, construction, automotive and packaging.
Alongside the two-component mixtures, Covestro presents a single-component chlorinated rubber in different versions for contact adhesives with high adhesion strength, resistant to corrosion and scaling. Therefore it is indicated in contact adhesives in the assembly of laminates for worktops or building panels. Thanks to the low content of carbon tetrachloride (CC14), the material meets all regulations globally.
The advantages of Covestro solvent-based adhesives are:
- high strength and resistance in lamination
- versatility: adheres to most substrates, including wood, metal and plastic
- High quality: with high purity and low volatile content
- durability: resistance to chemicals, atmospheric agents and UV rays.
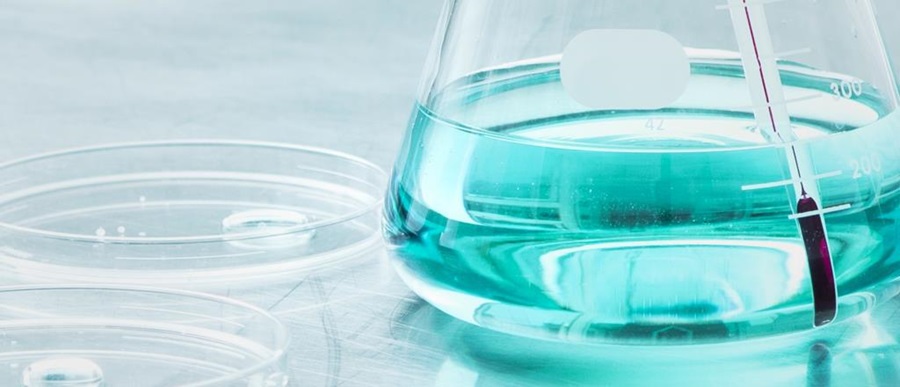
Materials for water-based adhesives and coatings
The demand for more environmentally friendly adhesives is pushing the market towards water-based adhesives. Polyurethane dispersions are an important step in reducing emissions in the processing of adhesives. Another aspect is also safety at work because, unlike solvent-based systems, there are no risks of fire and explosion and consequently expensive investments in ventilation, safety and recycling of solvents can be avoided. The water acts as a vehicle and not as a diluent or polymerizer, in fact we speak of dispersions of polyurethane particles in water, and when it evaporates it is the polyurethane that acts as an adhesive.
Covestro has a wide range of aliphatic polyurethanes which differ from each other in viscosity and molecular weights so as to be able to obtain specific adhesives for different needs. The aqueous colloidal dispersion of the 2-chlorobutadiene polymer has a high crystallization rate and is therefore very suitable for the footwear, construction, furnishing (mattresses and pillows) and automotive sectors. On the other hand, the high molecular weight anionic polyurethane dispersions are characterized by a strong cohesion between the molecules and therefore are the most suitable for resistant and high-strength adhesives indispensable in construction or for furniture but also in applications on PVC that contain plasticizers. Finally, an aqueous dispersion of anionically modified polyurethane can be used, which is very suitable for bonding activated by heat which must have good resistance to temperatures. All water-based adhesives can be enhanced and improved by additives. In Covestro, an amorphous silicon dioxide was studied which improves the rheological properties of deformation and viscosity.
Aqueous dispersions of polyurethane give adhesives:
- sustainable: with low solvent content and reduced emissions
- adaptable: with different viscosities and molecular weights meet specific adhesive requirements
- modifiable: with additives the physical qualities can be improved to facilitate use and spreadability.
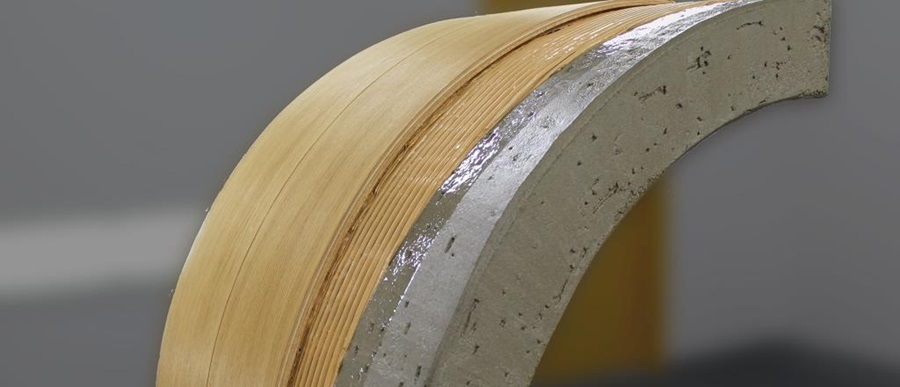
Materials for reactive and thermo reactive adhesives
To facilitate the application, storage and ultimately the effectiveness of adhesive materials, amorphous polymers activated by a reactant or by heat are used. Through the correct reagent it is possible to precisely control the behavior of the adhesive during processing and create a solid and stable bond between the layers to be bonded. Reactive adhesives can be mono or bicomponent and in the Covestro catalog you can find a variety of polymers suitable for every type of industry and application:
- polyether polyols, including diols and triols
- polyester polyols
- polycarbonate diols
- monomeric TDI
- monomeric and polymeric MDI polyisocyanate
- aliphatic polyisocyanates
- prepolymers
The thermo reactive adhesives are are high quality heat activated polyurethanes. They have the advantage of not being sticky and of being able to be distributed on the surface to be glued without fear that they will lose effectiveness over time. The crystallization action operated by the temperature can be done subsequently according to the production needs. Polyurethanes come in the form of microgranules that can be solubilized, can also be sprayed and used with a wide variety of materials.
This type of stickers are:
- strong with adhesion maintained over time
- resistant to heat and deformation
- easy to use in application and solidification
- customizable for different applications.
Hot melt
Widely used in industry or even in consumer products, hot melt adhesives are enjoying growing success. They can be made of different polymeric materials, but all of them have the characteristic of being in a solid state that are melted in the bonding process and then solid again at the moment of cohesion. The end result is a strong, economical and safe bond. The polymers do not contain solvents so they are non-toxic and also completely reusable. Covestro presents a material for hot melt in non-reactive polyurethane material that can be worked in a veil, in powder or in sheets and are used mainly in the footwear and textile industries.
There are also reactive polyurethane hot melts. With the addition of isocyanate, after the solidification phase there follows a reaction with the humidity of the air with the free NCO groups and a cross-linking is created which makes the bond extremely resistant to heat and chemical agents. Given the physical and mechanical characteristics, reactive hot melts are used in electronics, transport, wood and clothing.