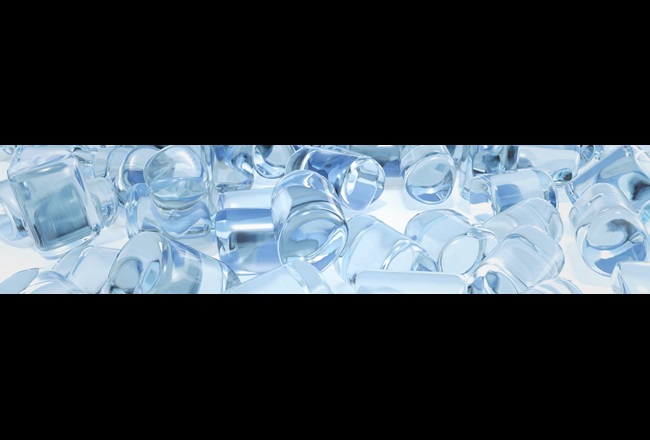
Thermoplastic polyurethane
The thermoplastic polyurethane
Like many other plastics that originated from the early polymerizations of the 1930s, thermoplastic polyurethane (TPU) is also part of everyone's daily life. In fact, this material, which arises from the polymerization of a di oil and an isocyanate, gives rise to numerous applications in every field.
The versatility of TPU is given by the possibility of intervening on the quality of the physical bonds of the polymer and obtaining blends that can be adapted to multiple uses. In the thermoplastic polyurethane chain, formed by an alternation of rigid and flexible segments, it is possible to vary precisely the quality of the sequences. In this way, more or less soft materials are obtained and the hardness or resistance to shocks, abrasions and tears, or to atmospheric and chemical agents is calibrated. To these features are added the ease of processing and the possibility of being subjected to subsequent processes such as sterilization, welding, painting, printing or cutting.
Precisely the versatility of thermoplastic polyurethane suggests a further growth in demand in the next five years of approximately 7% per year. The most affected industry will certainly be the footwear industry because the shoe has numerous components made of TPU. But also all plant engineering will see the demand for thermoplastic polyurethanes grow, especially in Asian countries which are consolidating and increasing their industrial infrastructures.
The great knowledge of the TPU material and production processes has made Covestro one of the worldwide referents for companies that want thermoplastic elastomers easily workable with various molding methods, which have high durability and flexibility, and are ideal for a numerous range of applications.
TPU: a versatile material
The soft segment of the TPU can be a polyether or polyester type poly oil. Polyester gives TPU good tensile and flexural properties, resistance to abrasion, solvents and high temperatures. However it is not resistant to hydrolysis. On the contrary, polyether withstands contact with water and air well, maintains flexibility even at low temperatures and has good tear and tensile strength.
It can be understood that as the precursors of the polymeric blend vary, the physical and chemical characteristics also vary. For this Covestro actively collaborates with companies to obtain a thermoplastic elastomer that responds exactly to the production requests for a specific component, in a consolidated practice of proximity to its commercial partners and continuous research of innovative products.
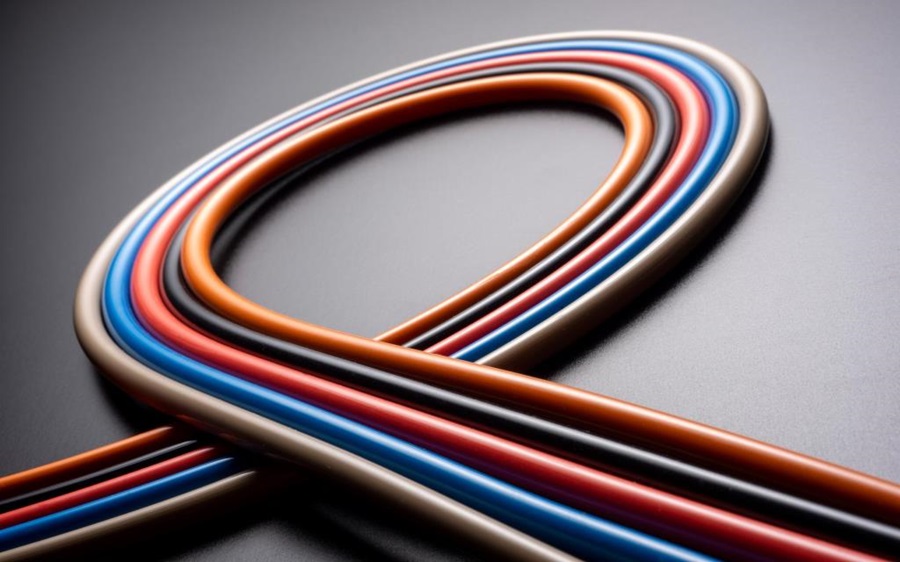
The physical and chemical characteristics of high quality thermoplastic polyurethane
From a mechanical point of view, Covestro has TPUs characterized by a high tensile and breaking strength that can compete, if not exceed, with the durability of high quality steels. Tear-resistant and tear-proof materials have been developed.
Resistance to chemical agents influences the choice of material especially in the construction of components that must be in contact with specific fluids such as acids or alkaline solutions, saturated hydrocarbons, aromatic hydrocarbons, lubricating oils and greases and solvents. Resistance to microbes, hydrolysis, UV rays and ozone can also be tested. In this context, polyurethanes show very variable behaviors that must be carefully evaluated from time to time.
If heat is the method for molding elastomers through extrusion or injection molding, the subsequent temperature resistance can be a discriminating factor in the choice of polymer blends. To predict its performance, TPU undergoes numerous stress tests. Higher quality thermoplastics expand with increasing temperature but contract again when the temperature drops back to their original shape. If the polyurethane is reinforced with glass fiber, there is an expansion of just 20%, with a coefficient of thermal expansion that becomes similar to that of aluminum or steel.
Like other organic compounds, polyurethanes are also combustible. Flammability is affected by environmental conditions such as oxygen concentration or material thickness. On average, the high quality TPU has an ignition temperature between 350 and 400 ° C and an auto ignition temperature between 450 and 600 ° C and meets the international automotive standard ISO 3795 (FMVSS 302).
High performance TPU for medical use
Thermoplastic polyurethanes generally have an opaque, almost milky appearance. Some elastomers are able to maintain transparency if the component does not exceed 2 millimeters, and also in this case the transparency depends on the working conditions in which it is found. Poly oil also determines optical properties: Polyether TPUs tend to be more transparent than polyester TPUs. In some applications, transparency combined with the flexibility of polyurethane is essential. Think of the protective films that must maintain an unaltered appearance over time or even more of the components for medical equipment. In this sector, thermoplastic polyurethanes offer a unique combination of different properties that position themselves between rubber and rigid thermoplastic materials. Covestro has a specific TPU for medical equipment in its portfolio. The studied mixtures have excellent transparency, chemical resistance to detergents and sterilization processes, transparency and resistance to yellowing due to UV rays. Its flexibility can be varied for use in medical devices and component housings as well as connectors. The polyester-based variant finds valid application as a coating for soft-touch handles or for the extrusion of sanitary pipes and ducts. If based on polyether, it has greater resistance to hydrolysis and is perfect for reinforced tubes and cannulas but also for films dedicated to the transdermal administration of medicines.
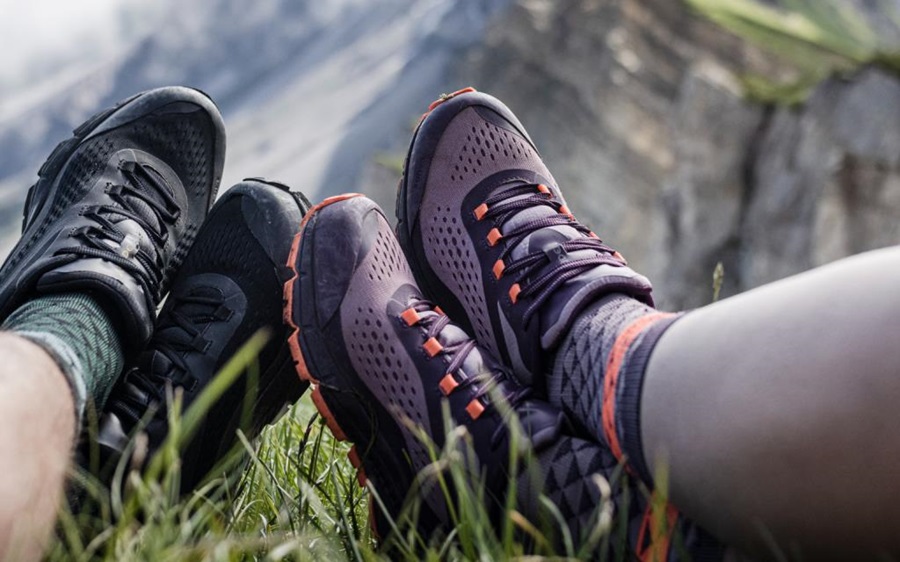
Low carbon footprint thermoplastic polyurethane
The spread of thermoplastic polyurethane in everyday applications is pushing end consumers to ask for ever safer and more sustainable products. Car interiors, fabrics, shoes, medical devices: all of these objects contain thermoplastic polyurethane and are often in direct contact with the skin.
Replacing fossil raw materials with others from renewable sources is a concept that is making its way into the markets and that brings tangible competitive advantages to companies attentive to this demand. Covestro is a pioneer in the search for sustainable polymeric materials and attention to environmental values and the circular economy is a fundamental part of its vision and mission.
The new biobased thermoplastic polyurethane uses up to 60% of renewable raw materials (the variability is given by the required hardness), in particular succinic acid and propanediol come from biomass. While maintaining the performance of a fossil-based TPU, including in terms of resistance to oils, greases and solvents, this new material reduces the carbon footprint by 20%. It is another step for a chemical production that respects the principles of the circular economy, as Thorsten Dreier, head of TPU and film activities at Covestro explains:
"In the long term, Covestro wants to direct its entire production and product offering to the circular concept. A crucial aspect of this program is the increased use of alternative raw materials, for example obtained from biomass, in line with the demands of our customers".