With innovative production processes, raw materials increasingly sourced from non-fossil fuels and an increasing share of renewable energies, Covestro is working to become fully circular and reduce the environmental footprint of its production of high-quality polymers for the production of plastics, while at the same time promoting innovative recycling technologies to reintroduce recovered waste back into the value chain as a valuable resource. Covestro aims to achieve climate neutrality by 2035 for its own emissions (scope 1), for external energy sources (scope 2), but also for greenhouse gas emissions related to upstream and downstream processes in the supply chain (scope 3), which account for 80% of the company's total greenhouse gas emissions. Getting there is far from easy. But by working together, anything is possible.
According to the company’s mission statement "to make the world a brighter place", Covestro in Italy is working to foster sustainability and make plastics manufacturing fully circular. The company is aiming for climate neutrality by 2035 for its own emissions and for external energy sources.
Closing the plastics loop
Covestro has identified solutions for industrial development and more sustainable growth. In this process, advancing circularity should become a guiding principle for the economy and society globally.
Italy is known as a country of beauty, design, and art. Covestro wants to honor this legacy and imagine a future that combines innovation and sustainability. At the Filago Color and Design Center (CDC), designers and manufacturers can study how to develop solutions for products that are beautiful to look at, functional but also recyclable, and fully circular. Sustainability is not easy to achieve. But possible.
Alternative raw materials for a sustainable future
Biomass, recycled used materials, green hydrogen – the raw materials of the future. Going forward, Covestro aims to make plastics out of alternative raw materials and thus make production more sustainable.
In 2022, the Filago site received ISCC PLUS mass balance certification, an internationally recognized system for sustainability certification of biomass and bioenergy.
This certification guarantees the traceability of recycled or bio-based raw materials throughout the supply chain. Covestro has adopted certified mass balance for bio-based polymerization raw materials that deliver the same quality as virgin raw materials but have a lower carbon footprint.
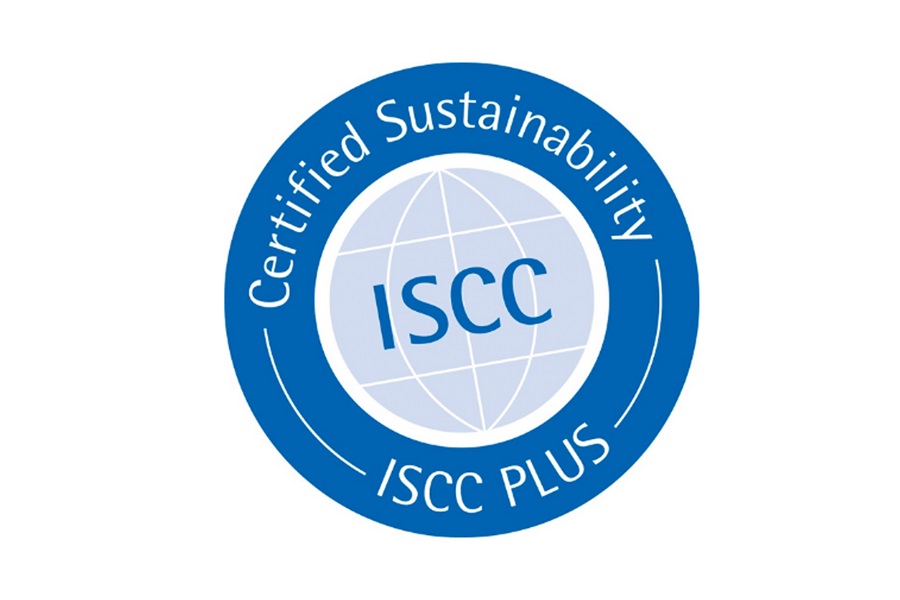
Promoting recycling with new technologies
Covestro recently announced its goal of becoming carbon neutral by 2035. The Filago site is also contributing to the achievement of this ambitious goal through numerous projects that aim to improve the recycling process for plastics and reduce the carbon footprint in the production of polymers.
Covestro has started producing some materials using mechanically recycled raw materials. Strategically, the Engineering Plastics business unit has defined an investment plan over the next ten years to increase the production capacity of recycled materials. The Filago site could become part of this investment plan.
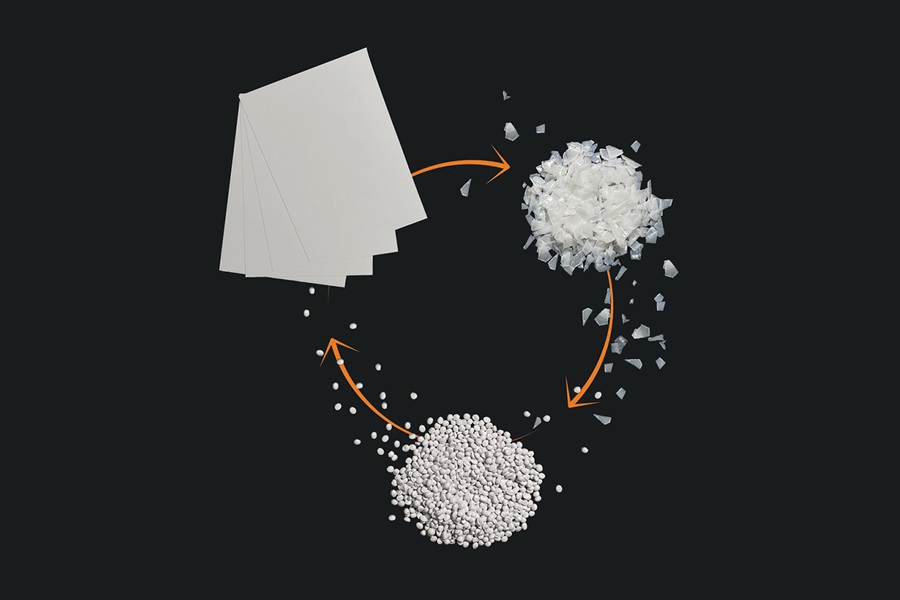
Higher value, less input
Resource efficiency means using the Earth's limited resources sustainably and thus minimizing their impact on the environment. It allows us to create more with less and deliver higher value with less input. Covestro is committed to continuously improving its production processes and energy supply.
For many years, Covestro has equipped all its electric motors with inverters to reduce their electricity consumption. Inverters with the highest efficiency class are fitted on all new installations and every time a motor is replaced.
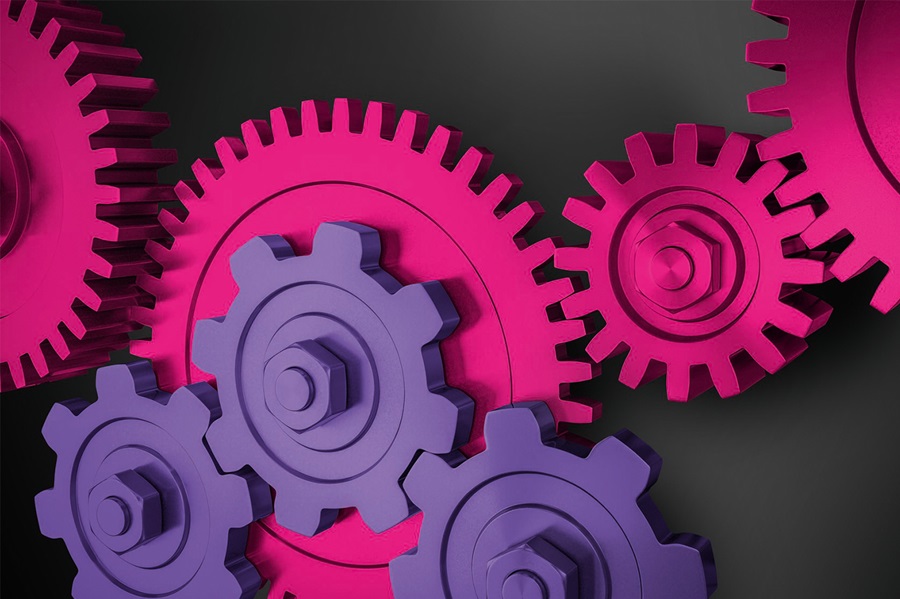
At Filago, Covestro is analyzing the thermoregulation of extruders, the cooling of motors, heat recovery from the various extractions (fume/dust extraction/towers/RTO) and inputs (adiabatic coolers/fans) to reduce energy consumption. Initial successes have already been achieved: The heater now uses 24% less energy per year. But that’s only one benefit since the heater’s water consumption has also been reduced by 87% on an annual basis. Now, Covestro is aiming for 90% and its goal is to make thermoregulation even more efficient.
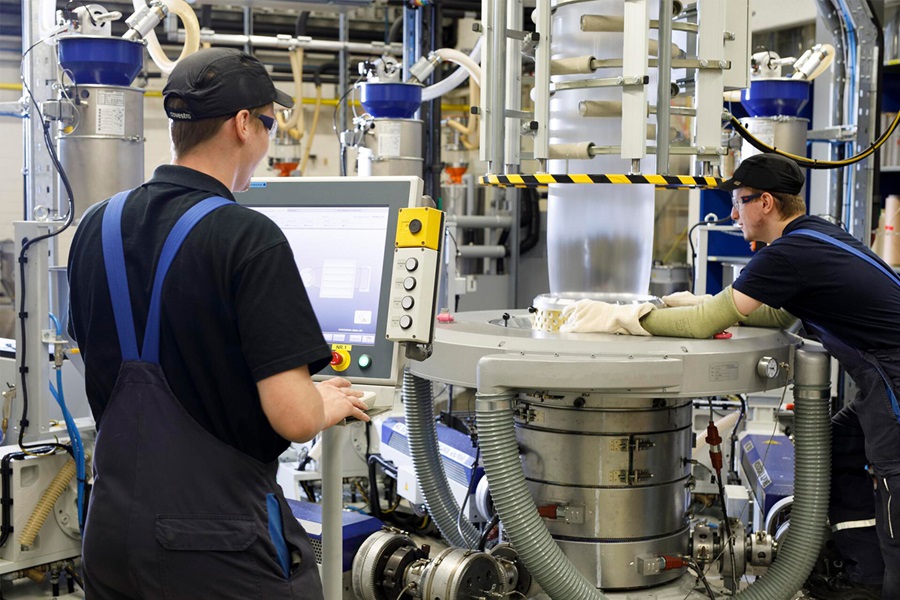
In 2021, Covestro implemented a project that reduced total water use by 30% through optimizing cooling tank management. Two other projects are currently underway, one involving the recirculation of water from vacuum pumps, the other the reuse of tank cooling water.
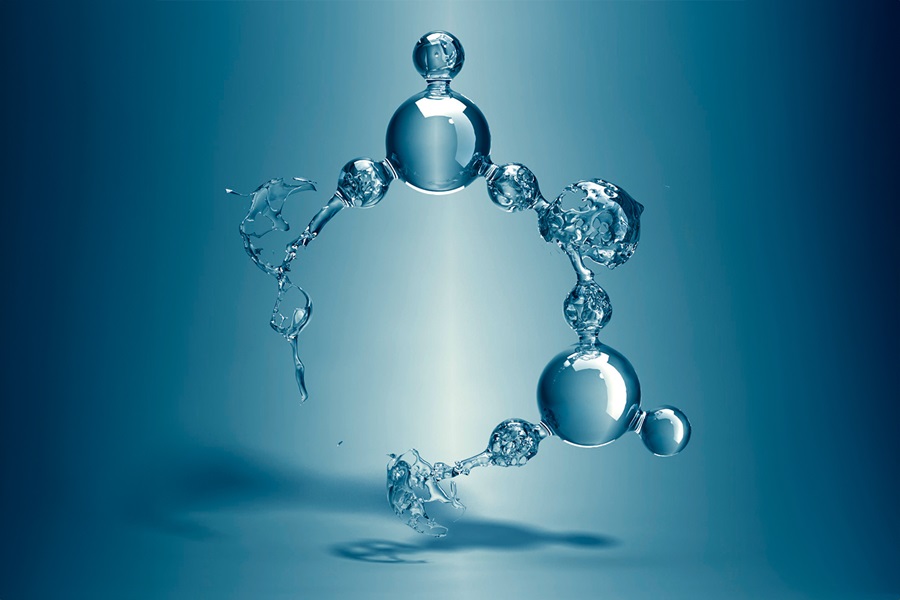