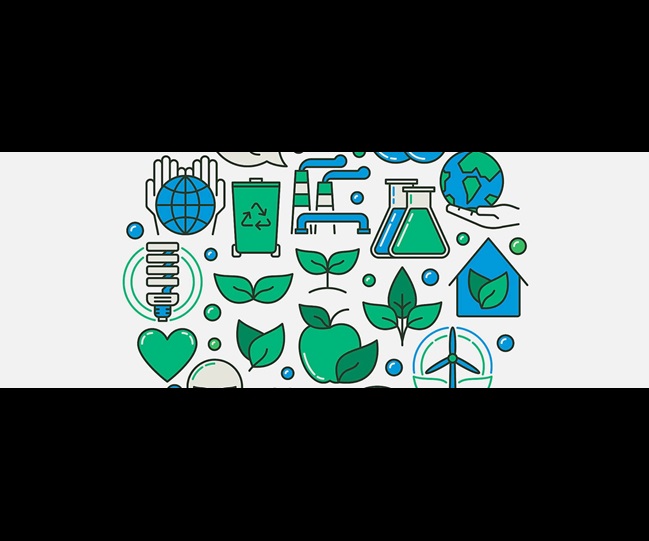
Innovative Recycling – More Reuse, Less Plastic Waste
Plastics are the materials of our time. They help us cope with global challenges, such as aligning economy and society with climate-neutrality, developing new mobility concepts, or addressing the growth of the world’s population and making our cities more livable.
However, in order to achieve a truly sustainable future and protect our environment in the long run, our attitude towards consumption and understanding of plastic waste – and waste as a whole – must change. Since 1970, global resource consumption has more than tripled. The natural resources for the whole of 2020 were already exhausted after eight months. At the same time, humanity does not utilize products in a sustainable way. According to a scientific study, only around 9 percent of all plastics manufactured between 1950 and 2015 have been recycled.
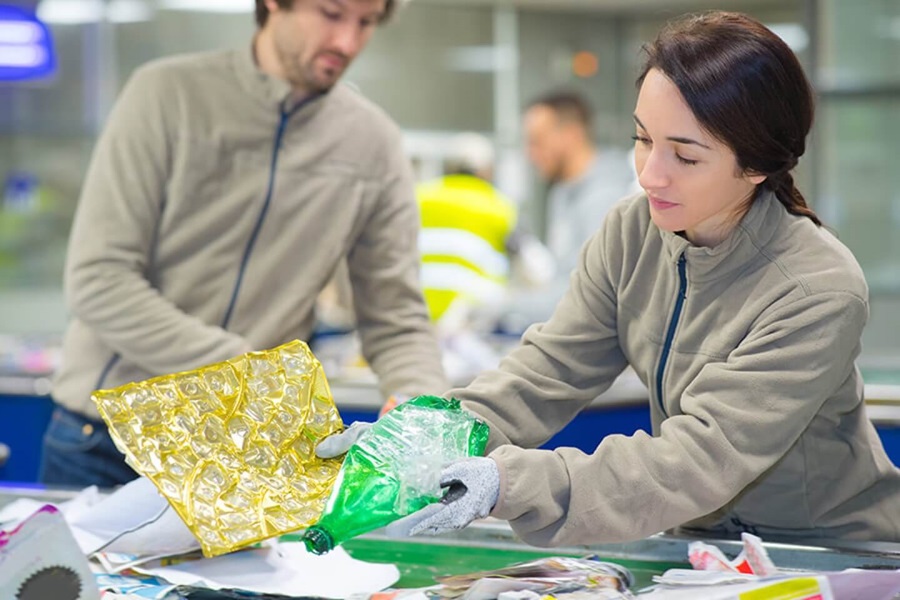
This must change. Produce, consume, dispose – this pattern has had its day, particularly in regard to plastics. They must be used more and for longer periods of time. And at their end of lives, they should be systematically and effectively reused and recycled in large quantities.
However, much remains to be done to achieve an effective and resource-efficient circular economy. For example, waste recycling systems and solutions must be improved or even set up across the world. Currently, about two billion people – one quarter of the world's population – do not have access to regular waste disposal.
Change can only succeed if all market players work closely together. The plastics industry can and wants to play a decisive role in this – for example in the Alliance to End Plastic Waste.
Covestro Promotes Recycling
As a pioneer of the circular economy, Covestro wants to promote plastic recycling. In particular, we aim to develop new technologies or innovations and make them marketable as quickly as possible. To this end, we have set up more than 20 research and development projects. We are pursuing a broad technological approach in order to meet the diversity of products and markets.
As we develop these new plastic recycling technologies, we are paying particular attention to energy efficiency. This way, we reduce the carbon footprint of our products and make our business more sustainable. At the same time, we are working to develop new circular business models with customers and partners.
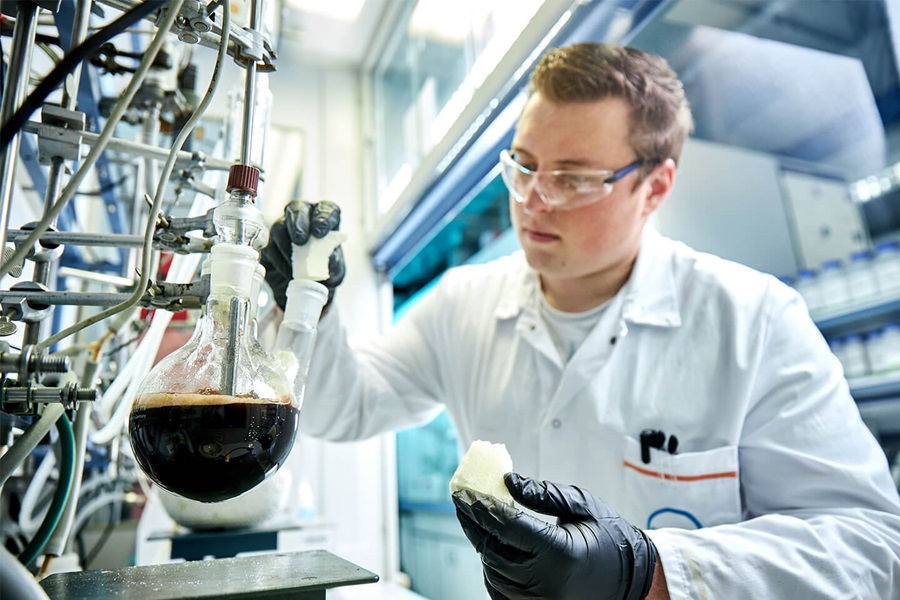
Comprehensive Technological Approach
Due to the large bandwidth of plastics, different recycling technologies and technological diversity are necessary - in addition to the established mechanical recycling the relatively new chemical recycling.
Chemical Recycling
In these processes, plastics are split chemically into their original molecular forms so that they can eventually be processed into entirely new plastic materials. Chemical recycling is the only sensible way to recycle certain plastics. It is therefore necessary to promote and develop chemical recycling as a supplement to mechanical recycling. This also requires the right political and regulatory framework.
There is significant demand for more development in chemical recycling – and this is where Covestro can provide its core chemical expertise. Our company has already achieved an important success: We have developed an innovative technology to chemically recycle soft polyurethane foam in mattresses. This makes it possible to completely recover the two core raw materials used in polyurethane. At the beginning of 2021, a pilot plant at our site in Leverkusen, Germany was put into operation in order to further advance the process.
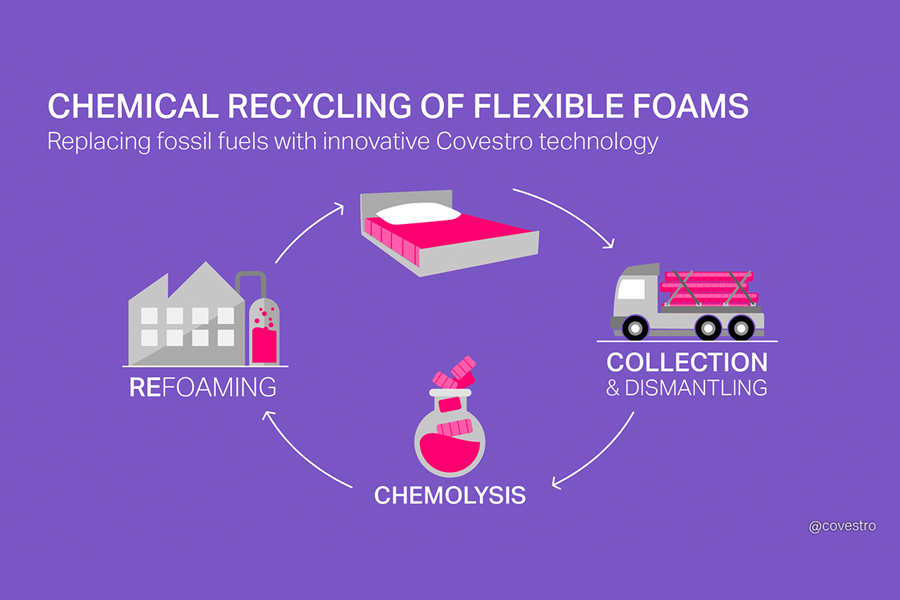
One type of chemical recycling is called enzymatic recycling. Here, used products and waste are broken down into their chemical constituents using enzymes, thus producing new recycled raw materials that can be reused. And finally, in pyrolysis, material is split into small molecules using very high temperatures. These molecules are often used again at the beginning of manufacturing processes.
Mechanical Recycling
In these processes, waste materials are recycled into "new" secondary raw materials without changing the base structure of the material. For example, after sorting and processing, plastic is crushed into granulate. This can be melted down and made into new plastic.
One of the ways Covestro uses mechanical recycling is to transform water bottles, into high-grade plastic components for electronic and household appliances as well as for car parts. For this purpose, we work together with the beverage manufacturer Nongfu Spring and the recycling company Ausell in China. The goal is to recycle one million polycarbonate bottles per year.
Design for Recycling
It is important to design plastics as recyclable materials from the very beginning, thereby protecting the environment. Covestro is also active in this field.
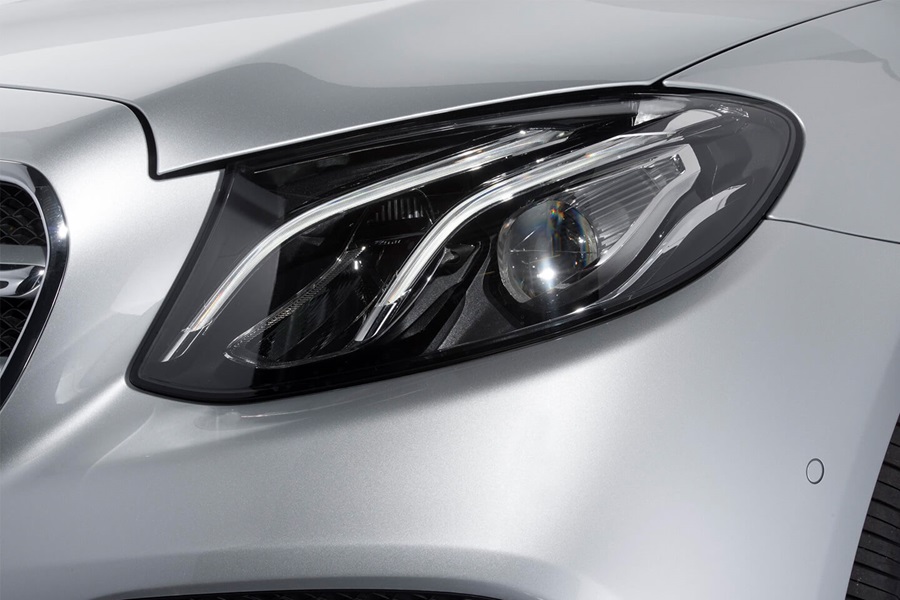
We have developed a concept for car headlights that are made only of polycarbonate and no other plastic. At the same time, there are significantly fewer individual parts than in conventional models. This permits simpler recycling because the separation, sorting and storage of the components is less complicated. Specifically for the electrical, electronic and household appliance industry (EEA), our company has published the "Circular Design Guidebook" together with the consulting company REnato lab. This booklet will help designers and developers make their next-generation products more circular.